3D printer: Difference between revisions
Line 175: | Line 175: | ||
|[https://de.anycubic.com/ Anycubic] | |[https://de.anycubic.com/ Anycubic] | ||
|Kobra 2 | |Kobra 2 | ||
| | |309 | ||
|250x220x220mm | |250x220x220mm | ||
| | | |
Revision as of 10:21, 24 June 2023
Introduction
This article shortly introduces 3D printers and provides some advice on selecting a printer. The original article, created many years ago, listed many printers, but I stopped upgrading systematically around 2016. The old version is still around. There are no endorsements, since I only owned a RapMan (2010), a fabbster (given away), a Creality (2015, given away), four different Felix printers (1.0, 2.2, Pro2 and Tec4.1 (I still use the latter two), a Fokoos Odin-5 F-3 (2022, bought for 200 Euros on sale). I also use Prusa mini and I3 printers in our fablab.
According to Wikipedia, retrieved 11 April 2023, 3D printing or additive manufacturing is the construction of a three-dimensional object from a CAD model or a digital 3D model.[1] It can be done in a variety of processes in which material is deposited, joined or solidified under computer control,[2] with material being added together (such as plastics, liquids or powder grains being fused), typically layer by layer.
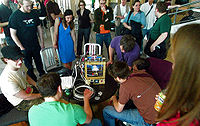
See also:
- 3D printing (explains some principles).
- 3D food printing
- Fab lab (for a wider technical picture)
- 3D printers in education and fab labs in education (for a wider picture in education)
- Printer-specific articles: Felix, RapMan, and Fabbster
- Software (listed below)
- Hobby milling (an alternative subtractive technology)
- (Micro) Fablab TECFA, our own little gear
- Slicers and user interfaces for 3D printers
3D printing technology
The most popular 3D printing techniques are:
- Fused deposition modeling (FDM), also called Fused Filament Fabrication (FFF). A typical example of the first available low cost kit that required a few days of assembly was the RapMan. As of 2023, entry level printers are cheap (around 300 Euros) and are assembled fairly quickly. Consumer-grade quality machines cost around 1000.
- Stereolithography (SLA): “is a form of 3-D printing technology used for creating models, prototypes, patterns, and production parts in a layer by layer fashion using photopolymerization, a process by which light causes chains of molecules to link, forming polymers.[1] Those polymers then make up the body of a three-dimensional solid.” (Wikipedia, Aug. 2017). SLA machines use a laser to harden selected areas.
- DLP (Digital Light Processing) works, like SLA, with resin. As opposed to a laser that will solidify very specific areas, a DLP printer projects an image onto the pool of resin which then hardens each layer, one at a time.
- Selective laser sintering (SLS): “an additive manufacturing technique that uses a high power laser (for example, a carbon dioxide laser) to fuse small particles of plastic, metal (direct metal laser sintering), ceramic, or glass powders into a mass that has a desired 3-dimensional shape” (Wikipedia, retrieved 14 October 2011)
- Syringue-based systems like the early Fab@Home can print Epoxy (composites), ceramics or food and these materials are pushed down with a piston.
Most hobby 3D printers use FDM, i.e. an extruder (i.e. a kind of gun) that heats up plastic filament which is then deposited layer by layer. They can print different sorts of Polymers. In the early years, the two following plastics were popular.
- ABS (used for Legos and car parts) is solid, but warps when printed a room temperature. I.e. it is difficult to print objects that have a larger than 4cm footprint.
- PLA (polylactic acid) is made of starch (i.e. plants). It doesn't warp, but it was not very solid and started deforming (melting) at relatively low temperature. As of 2023, more solid PLA filaments are available.
As of 2015 a much wider range of 3D printer filaments are available, including PET-G, PET, Nylon, TPU, TPEs, and various PLA-particle composites.
Type | FDM / FFF | SLA | SLS | Piston |
---|---|---|---|---|
Material | rolls of various types of plastic | Liquid resin | Various powder (only Nylon or similar for low end machines) | Anything that can be pushed down (e.g. chocolate or Epoxy resins or clay) |
Durability | OK (depending on type of plastic) | Low | High | depends on the material, very little for printed food :) |
Precision | 0.05 mm | high | good | |
Post-processing | Easy (except when dealing with support materials) | Treatment is required to improve solidity | Blasting is required to remove bits of loose powder | |
Freedom of forms | No.
Somewhat if soluble support is used in dual head printer. |
limited | yes | very limited |
Heat resistance | Depends on the plastic. E.g., popular PLA is starts weakening at 60 and melting at 160. PETG, and other popular plastic has a higher melting temperature. Some plastics like nylon are difficult to print but much more resistant | limited | good | |
Unit cost | very low (starting at 150, a good model is about 1000) | low | high | medium |
Material cost | very low to low (15-100 Euros/kg) | 30-250 Euros / litre | 100 - 1000 Euros / kg. |
The opposite of additive manufacturing is subtractive manufacturing that takes away material from an initial form. These alternative technologies include:
- Laser cutting, a fairly simple to use technique for creating "flat" 3D objects by cutting "sheets" like wood or plexiglass. One can create designs that involve sticking or gluing components together.
- Milling, a process where parts of an object (e.g. a cube) are removed by drilling. For example, parts of car motors are produced like this. Milling is a fairly dangerous process, however hobbyist models that carve out from plastic or wood are safe to use in a classroom for example.
Filement printer features you should you look for
Must have features:
- A strong extruder including a good filament intake system (you should be able to walk away from the printer and be sure that plastic is always extruded, even after 20 hours or printing). Newcomers don't often get the fact, that even a fairly small piece takes many hours to print !
- A good board and firmware (as above, there should be no mistakes, i.e. a print head that stops moving at some point)
- A heated platform up to 80 degrees at least
- Ability to print 0.1mm layers accurately
Nice to have features:
- Support for different nozzle sizes up to 0.8mm (easy changing plus useful information on supported nozzles and how to change them)
- Support for multiple types of plastic, in particular PLA and PET-G, but also some stronger plastics like ABS or Nylon (for some, this is a must-have feature). Some people also want to print with flexible polymers, i.e. TPU or TPE. That requires a direct extruder where the motor sits on top of the nozzle (i.e. so-called Bowden extruders are not very suitable for TPU and not suitable for TPE)
- Extrusion and printhead movement speeds as slow and as fast as possible. Typically the first layer should be printed at 10-15mm/s but prototype quality should be printable at 150mm/s.
- A heated chamber (or at least a closed box) for printing plastics that warp, e.g. ABS.
- Accuracy (both detail and movement) down to 0.1mm resolution if possible
- Two print heads (for printer either two color models or designs that need support. In the latter case, there exit soluble plastics.
- Included easy-to use printer control software
- Support for a good machine code generation software (i.e. a slicer). Most printers work with open source slicers but the vendor should nevertheless provide some good standard settings.
- Support for standard RepRap g-code (in order to avoid slicer software lock-in)
- Control hardware/software that allows to pause/resume a print and to manually extract filament.
- As many standard hardware parts as possible (this will allow for quick replacement) and allow you cope if the company goes out of business. This includes the control board.
- Use of open source software for controlling the printer. Except for very few exceptions, opensource solutions like Repetier Host are simply better since you can still use your printer after the company and its software go out of business
- Automated bed leveling or model correction. Adjusting the bed (1-2 sheets of paper distance from printhead to bed in every position) is something that beginners have trouble with.
- A wide printing area (as wide as the objects you plan to print). 25x25x25 is OK as of 2023.
Comparisons
Comparing 3D printers is very very difficult for several reasons:
- Some do better than others with respect to different sorts of objects. Do the benchmark pieces represent what you would like to print ?
- Calibration is essential. Only a real expert can get the most out of a machine.
- How do you weight various factors ? (Reliability, smoothness/accuracy, min. layer size, speed or less obvious stuff like does the first layer stick, warping, dealing with overhangs, stringing)
- How do you account for the interaction between slicing software and printers, and between slicing parameters and printers ?
On of the first serious comparisons was done by Make Mag in nov 2012. One of my printers (the Felixprinter 1.0) came out ok. Nevertheless the author complained about assembly that was more difficult than expected and glitches with some delivered parts (like calibration of the stepper motors) and he is right to do that. However, why compare a non-assembled printer with assembled ones. I bought mine assembled (400 Euros extra) and it worked out of the box! In addition, the testers used default settings of the slicer software. Had they selected a different profile they would have obtained widely different results. I was able to print a test design that failed without problems. The Make Mag test was serious, but far from perfect. - Daniel K. Schneider 17:53, 22 November 2012 (CET)
Do not trust marketing hype. In any case, filament printers do have inherent flaws that no design can solve. Only trust reputable online sites (most receive something in exchange for rewiewing). Also, understand that some cheap printers start degrading after a few weeks and that others have poor quality assurance (i.e. some machines work fine but others need to repaired when you open the box).
Fast 2023 FDM machines
I am looking into these models right now and may buy one. By the end of 2022 very fast "coreXY" FDM printers did appear on the market or were announce for Q2 or Q3 of 2023. An other options are IDEX printers where two extruders can work at the same time on copied or mirrored same objects.
Since I hate waiting a full day for a moderately large bag of LEGO or DUPLO compatible bricks I am interesting in getting one of these model and would print with a 0.6mm nozzle or larger.
Some of these printers may require minor modifications, e.g. better PEI print plates (e.g. this for the Bambu] or better nozzles. All probably require verification and some tuning after the transport.
Brand | Model | Cost (Euros) | Print volume & (machine volume size) | Propriety | Extruder(s) and AMS | Resolution & hot ends | Max speed and flow | Plate and Levelling | Trouble detection & recovery | Filaments | Other | Evaluations |
---|---|---|---|---|---|---|---|---|---|---|---|---|
AnkorMake | M5 | 850 | 235x235x250 mm | ? | Ultradirect extruder | 0.4mm nozzle, 0.1-0.35mm, 260 deg.
|
250mm/s standard speed. | PEI-Coated Soft Magnetic Steel | Camera with AI | ABS, PETG, PLA, TPU | Noisy,
app to view camera and pilot |
Good budget printer. Not coreXY |
Anycubic | Kobra 2 | 309 | 250x220x220mm | Direct extruder | 0.4 nozzle (replaceable) 260 deg. | 250 mm/s (150 recommended). Benchy in 30 minutes. | Magnetic Flex plate, Auto-levelling | PLA/ABS/PETG/TPU | New as of June 2023 | |||
Bambu | P1P | 660 | 256 × 256 × 256 mm
(size = 386*389*458 mm) |
yes | Direct extruder | 0.05 - 0.35 mm, all metal 0.4mm nozzle (300deg) |
|
PEI-coated flex plate, Lidar levelling | Simple version of X1. Medium noisy,
app to view camera and pilot |
Was developed as low cost version of X1. Mixed reviews | ||
X1 Carbon | 1130 (1370 AMS) | 256 × 256 × 256 mm
(size=389 x 389 x 457 mm) |
yes | Direct extruder
Optional (wasteful and not TPU compatible) automatic materialsystem (AMS), 90 sec to change color |
0.05mm, all metal 0.4mm hotend (300deg). Larger nozzles can be added with extra work only. | 500 mm/s max, 250mm/s default. 32mm3/S throughput. Benchy in 16min30s | PEI-coated flex plate,
Lidar leveling, 120 deg. |
Spaghetti detection through camera | PLA, PETG, TPU, ABS, ASA, PVA, PET Ideal for PA, PC, Carbon/ Glass Fiber Reinforced Polymer | Noise level: about 50 (sometimes more).
App to view camera and pilot |
Mostly good reviews some negative because of various problems. All proprietary is also criticized.Very (!) wasteful AMS. | |
Creality | K1 (May 2023) | 650 (without options?) | 220*220*250mm
(size = 355*355*480mm, 12.5kg) |
? | Dual gear light-weight direct extruder (190g) | 600mm/s,
flow=32mm3/s |
Auto-leveling. Optional Lidar | Filament sensor. Optional camera | ABS, PLA, PETG, PET, TPU, PA, ABS, ASA, PC, PLA-CF, PA-CF, PET-CF | none so far | ||
K1 MAX (summer 2023) | 1000 | 300x300x300
(size=435x462x526mm, 18kg) |
? | Dual gear direct extruder | 0.1 to 0.35 mm with a 0.4mm nozzle. | 600mm/s. 300mm/s typical (correct
Benchy in 13min) |
Flexible build plate, leveling with
Lidar |
AI camera, filament sensor, power-loss recovery | most | WIFI/USB/Ethernet | none so far | |
Prusa | MK4 | 900 Kit
1200 assembled (incl VAT) |
250x210x220 mm
(size=500×550×400), 7 kg. Optional enclosure for 350+ |
no | Direct drive extruder. Optional MMU | quickswap 0.4mm nozzle (others on option)
0.05-0.30 mm 300 deg. |
20 min benchy in test for future upgrades. | PEI spring steel sheets, Mesh bed levelling with load cell censor | Filament sensor, power panic. | PLA, PETG, ABS, ASA, Flex, HIPS, PA, PVA, PC, PP, CPE, PVB, NGEN | WIFI/Ethernet
medium noisy, silent with enclosure |
none so far |
XL | 2500 ? (1 extruder) | 360x360x360 mm
(size=800×800×900mm) |
no | Direct extruder (5 optional).
Hot swappable noozzles |
0.05mm
(300 deg) |
Mesh bed levelling | Good support. Excellent reliability. Input shaping for speed printing is not available as of April 2023. | |||||
Makerbot | Method | 4000 to 6000 | 190x190x196mm.
152 x 190 x 196 (double extrusion) |
yes | 1-2 extruders | 300deg | ? | ? | PLA, TOUCH, NYLON, PETG. Method X supports ABS and more | Expensive, Various models | ||
Snapmaker | J1 | 1600 | 300x200x200
160x200x200 (copy) 150x200x200 (mirror) 30kg (size=490x445x443) |
Independent dual extruder (IDEX).
20 seconds to change color |
0.4 nozzle (300 deg) | 350mm/s for 0.1 layers. 200m/s for normal layers.
(22 min for 2 mirrored benchys). |
Double-sided PEI Glass Plate. | no camera | Most, including TPU and nylon. | slient, | Good quality parts. Default slicer not very good. Not as fast or large as competition. Only IDEX machine in this range. | |
Vivedino / Formbot | Troodon | 1000 | 300x300x400 mm (or 400x400x500 large)
(size= 600x680x610 mm, 28kg) |
no | Direct extruder | 0.4mm easy swap nozzle (0.2. to 0.8 on option), 0.05 to 0.3mm.
270 deg |
max: 500mm/s | PEI coated flex bed.
BLT touch sensor (36 points) |
most, including abrasives | This is a kind of Voron architecture | 95% assembled, requires some skills. | |
Voron | 800 to 1500 | 350x350x350mm (version 2.4). Other options are 250x250x250 or 300x300x300 | no | Direct extruder | 0.4 nozzle, 285 deg | Automatic leveling with inductive probe. | Voron is a design and is sold in the form of various kits. | Good (best current kit), but requires expertise to assemble and get it working. |
If you looking for a popular cheap machine, you could check out:
- Creality Ender-3 S (the Pro version is more expensive, but worth it, the Plus version has more build space)
- Artillery Sidewinder X2
- Anycubic Kobra
You can find these in many online shops. Prices can vary greatly at times. If you are low on budget, watch out for 50% sales, e.g. around 150 to 200 Euros.
If you are looking for a reliable, a bit more costly machine (out of the Box and staying), check out:
- Prusa mini or Prusa i3 MK3
Avoid expensive commercial brands that offer consumer machines with lesser functionality for higher prices, e.g. Makerbot Replicator.
History of consumer-grade 3D printers
Below, some consumer-grade 3D printers that made early history after 2005 where Adrian Bowyer launched the RepRap Project. Most links will be broken, since pages have been taken down or the companies went out of business.
Reprap 3D FDM printers
RepRap, a British project, is short for Replicating Rapid-prototyper. They all can be assembled from parts bought in various places. In 2018, there were several different Reprap Designs. The classic ones plus some other earlier designs are the following:
- Darwin. The design that inspired the first commercial Rapman and CupCake designs
- Mendel Overview (second generation Reprap)
- Prusa Mendel Overview (improved easier to build Mendel)
- Huxley Overview (travel sized mendel)
- Delta / Rostock
- RepRap Snappy (2018, most 3D printable printer).
All RepRap printers can built with spare parts available from many places. However, this requires good "bricolage" skills. For those who don't have these, there exist many commercial kits that are relatively easy to assemble and also fully assembled kits (see below).
Resources:
- RepRap wiki
- RepRap Official Blog (last post in 2014)
- RepRap Project (Wikipedia)
Candyfab printers
Candyfab was one of coolest projects in the beginning of DYI 3D printing. It did sugar sintering.
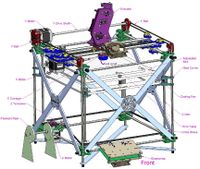
Bits from Bytes printers
Bits from Bytes did produce and sell Reprap derivatives, in particular the RapMan v3.11 (£750 / CHF 1270) we acquired in January 2010. It was assembled by end of Feb 2010 Read the RapMan article. The company is now dead, i.e. it was absorbed by 3D systems.
- Print area: 27 x 20.5 x 21 cm, not heated platform
- 3mm nozzle
- Resolution: x&y axis = 0.2mm, z axis = 0.7mm (roughly)
- Materials: ABS (warping for bottom surfaces larger than 4-5cm), "Hard", original translucid PLA (very different from "modern" processed PLA).
The Rapman was one of the first commercial kits for the RepRap v1 and it's probably one of the most beautiful designs. Assembly was rather difficult, but very well documented. All you needed was good reading skills. It did work, but did need what we could call "RepRap printing skills". Some design elements could be improved, in particular: filament intake (extruder), portability (after transport the structure may need adjustment), heated platform.
Fab@Home 3D printers
Fab@Home, is marketed as "personal fabricator". As opposed to RepRap designs, Fab@Home used a syringe system and could print a large variety of materials, including silicone, cement, stainless steel, cake frosting, and cheese. Hardware designs and software on their website were open source. This printer also included a dual syringe tool for printing two materials simultaneously.
Hardware:
- Fab@Home Version 2.0 - Kit for Single Syringe System cost was $2125 (oct. 2011). An assembled Fab@Home V1.0 - Assembled Two Syringe System would cost $3500
- Accuracy: Depends a lot on the materials, with a fine nozzle about 0.1mm in theory (+/- 100 micrometers according to the website).
Resources:
Makerbot printers
MakerBot Industries sold other RepRap-inspired designs. Like other Reprap derivaties, their 3D printers included a plastruder and an Arduino-compatible microcontroller and worked with several kinds of plastic, e.g. ABS and HDPE (milk-jug like). The founder of this company was also involved in the RepRap research project.
- A free design called CupCake CNC and and its current (2011) Ultimate. Makerbot will sell the parts. I don't know if there is any difference in design with respect to the Thin-O-Matic kit.
- MakerBot Thing-O-Matic® Kit (formerly called Cupcake?)
- Between $1225 and $1300 for the kit and à2500 fully assembled
- 3mm extruder
- 9.6 x 10.8cm print area
Later, this company developed closed sourced systems that became popular with institutional buyers. The company still sells expensive rather high-end machines.
Makergear
Makergear sold two kits as of oct. 2011. One is rather destinated to people who want to play with the Mendel Prusa design and maybe do creative modifications. The other, i.e. the Mosaic was more of an end-user product.
- Prusa 3D printer kit
- $825 for a complete kit
- 8 x 8" Heated Build Surface PCB
- Either 1.75mm or 3mm hot end (allowing to print either more precisely or faster). Most current printers feature a 3mm nozzle.
- supports both ABS and PLA
- Mosaic 3D Printer kit
- $999
- (Probably) fairly easy to assemble
Printrbot
Probably was one of the most popular 3D printers as of summer/fall 2012. S
- printrbot.com
- Open Hardware Design
- z axis: printhead moves up (not the platform)
- Heated platform that moves in the y axis (or x axis depending on how you look at it)
- Cheap, i.e. between $400 (smallest, print bed not heated) and $700 (largest)
- The large Printrbot PLUS has a 8x8in heated bed
- Claimed to be fairly easy and quickly to assemble
Documentation:
- backers at KickStarter
- Asssembly instructions
Ultimaker
As of Oct. 2011, the Dutch Ultimaker was the favorite open source design kit. It was (comparatively) fast, could print big and was easy to assemble compared to a RapMan for example. Ultimaker focused on speedy PLA printing and contributed to make this somewhat ecological filament the most popular.
Hardware:
- The Ultimaker 1 Kit costs EUR 1200.
- Reprap design
- It can print 21x21x22 cm volumes
- USB connectivity, drivers for Win/Mac and Linux
- 0.4mm nozzle The theoretical resolution: 0.0125 mm for the X and Y axis and better for the Z-axis. Don't know what the practical one would be.
- User-friendly feed mechanism
- No heated bed (?)
- Ultimaker 2 became a very popular machine in Fablabs, because of its good design, reliability and precision.
Resources:
Web services for 3D printing
There several companies who fabricate 3D objects from models created by the public. Typically, online 3D printing services also include a store where users can both upload and sell designs. Some sites also offer other manufacturing and commercial services and most also provide free resources for learning how to create things
Software and formats
Roughly speaking, the production pipeline looks like this:
- Model something or find a model
- (Merge/adapt models)
- Translate to a printable model, e.g. STL, AMF, OBJ
- Translate the printable model to machine code, e.g. g-code
File formats
The most popular file format was and still is the .STL file format: “An STL (“Stereolithography”) file is a triangular representation of a 3-dimensional surface geometry. The surface is tessellated or broken down logically into a series of small triangles (facets). Each facet is described by a perpendicular direction and three points representing the vertices (corners) of the triangle. These data are used by a slicing algorithm to determine the cross sections of the 3-dimensional shape to be built by the fabber” (The StL Format, retrieved 17:25, 24 June 2009 (UTC)). STL files can be created with most CAD programs. Alphaprototypes provides instructions for several popular CAD applications. More recent formats like 3MF are more versatile and can for example include color information.
3D Printing software
We distinguish between three kinds of "printing software"
- Preparation software will take a 3D model, allow you to make some adjustments (like repairing) holes, positioning and rotation and then output a clean printable format, in particular .STL files. The most popular software in that category in the early days was Netfabb Studio (now absorbed by Autodesk). As of 2023, most slicers include some automatic basic repair facilities.
- Slicer software will take as input an .STL model (or similar) and then produce machine code according to various parameters that you can set.
- Control software, can send print files to a printer and control the printer otherwise (e.g. manually move the print head, change temperature, etc.)
Some software can do all of these.
See: Slicers and user interfaces for 3D printers
Related EduTechWiki articles
In EduTechWiki, we did provide a few overviews and/or beginner's tutorials. However, most of these are not up-to-date, since there exist many better alternatives since the late 2010s. See the category 3D printing. For example:
- Printers
- Modeling software
- OpenScad beginners tutorial (3D modeling with code) and Doblo factory OpenScad routines for creating DUPLO/LEGO clones
- Sketchup 3D printable objects tutorial (3D modeling with this Google tool)
- Sculptris (3D modeling by sculpting)
- Meshlab for RapMan tutorial (translating file formats, mesh merge)
- Preparation and Slicing
- Slicers and user interfaces for 3D printers
- Netfabb Studio tutorial (positioning, dimensioning of STL files for printing, simple object creation/merge)
- Skeinforge for RapMan (G-code generation for the rapman) and G-code (overview)
- Netfabb engine for RepRap and Netfabb engine for fabbster build styles
3D objects can be found in various repositories
- 3D assets, See also the Fab lab and 3D printers in education articles which also includes bibliographies or reviewed articles and books.
Repositories
- See 3D assets
General Links
(needs updating, some links are over a decade old ....)
- Fundamentals: 3D Printing of Digital Models at graphics.com, excerpted from [Digital] Modeling (New Riders). This article explains how a commercial "powder-based" 3D printer works.
- 3ders.org “latest news and developments of 3D printing technology, and informations of 3D printers.”
- Which is the best 3D printer? Detailed list of low and mid range printers.
- 3D Printing (Explaining the Future, oct. 2011). Includes a review of both commercial and open source printers.
- Three dimensional printing Laboratory (MIT,last update 2000)
- The next Napster? Copyright questions as 3D printing comes of age by Peter Hanna, ArsTechnica, 2011.
- Fabbaloo is a blog with news about personal manufacturing and 3D printing. See for example their very good list of personal 3D Printers (Dec 2011).
- Planet Reprap - A RepRap blog aggregator
- Reprap development and further adventures in DIY 3D printing (Interesting blog)
- Open Design: Products in a networked culture @ Fabfuse 2012 (Good video talk by Ronen Kadushin / Vimeo)
- L’actu de l’Imprimante 3D, mostly in French.
- PRIMANTE 3D, site média spécialisé dans l'impression 3D
- 3D printing for beginners (Blog)
- FDM vs. SLS 3D Printing - What They Mean and When to Use Them (Sculpteo, 2015)
On wikipedia
- 3D printing
- additive manufacturing
- selective laser sintering
- fused deposition modeling
- laminated object manufacturing
Acknowledgments
- Pictures are reproduced without permission. I don't think that any non-open source Maker should complain. After all, these may help selling.