Fab lab: Difference between revisions
m (using an external editor) |
m (→Fab Labs) |
||
(155 intermediate revisions by 3 users not shown) | |||
Line 1: | Line 1: | ||
<!-- <pageby nominor="false" comments="false"/> --> | |||
Most parts of this piece have been written in 2011 and 2012 and some may need updating. | |||
== Introduction == | == Introduction == | ||
A '''Fab Lab''' (fabrication laboratory) is a small-scale workshop with computer controlled tools with the | A '''Fab Lab''' or ''fablab'' (fabrication laboratory) is a small-scale workshop with computer controlled tools with the aim to make "almost anything". ([http://en.wikipedia.org/wiki/Fablab Wikipedia]). | ||
Fab labs | Fab labs are a [[disruptive technology]]. In the same way that micro computers changed computing, desktop '''fabbers''' (fab lab machines) may change manufacturing, i.e. people can produce things at home or within small organizations. | ||
Fablabs are typically open to the public and should have a charter. Other types of collaborative workshops for making are maker spaces, hacker spaces, tech shops, fac labs, etc. A space with a lone 3D printer should not be called a fablab. | |||
The Fab Lab | Fab labs and 3D printers in particular will have a [[fab labs in education|certain impact on education]] including computer-supported educational technology. Examples of educational domains and applications are design teaching (in engineering or design schools), producing [[constructionist learning object]]s (manipulatives that may or may not be augmented with computer technology), and creation of replicas or augmented objects for [[museum learning]]. | ||
See also: | |||
* [[Fab labs in education]] (overview article with links and bibliography) | |||
* [[Digital design and fabrication bibliography]] | |||
* [[Constructionist learning object]]s and [[Fröbel gifts]], i.e. educational application areas with potential for desktop fabbers. | |||
* [[Tour de Fablab]] (under construction until december 2011) | |||
* [[Fablab TECFA]] | |||
* [[3D printing]] | |||
* [[computerized embroidery]] | |||
* [[hobby milling]] | |||
* Vinyl cutting ([[Silhouette Cameo]]) | |||
Fab labs can have different aims, e.g. the include ''rapid prototyping of industrial products'' or ''low cost and on-demand manufacturing from "open source designs" for both hobbyist and serious use''. Both purposes include an idea of empowering individuals to create devices that are adapted to specific needs. Fab labs also can be part of Do-It-Yourself (DIY) communities, cultures and projects. ([http://staceyk.org/hci.php Kuznetsov, 2010]) | |||
The [http://www.fabathome.org/wiki/index.php?title=Fab%40Home:Overview Fab@Home project] emphasizes freedom of design and innovation of a Solid Freeform Fabrication system: | |||
{{quotationbox|Universal manufacturing embodied as today’s freeform fabrication systems has – like universal computers – the potential to transform human society to a degree that few creations ever have. The ability to directly fabricate functional custom objects could transform the way we design, make, deliver and consume products. But not less importantly, rapid prototyping technology has the potential to redefine the designer. By eliminating many of the barriers of resource and skill that currently prevent ordinary inventors from realizing their own ideas, fabbers can “democratize innovation” [1,2,3]. Ubiquitous automated manufacturing can thus open the door to a new class of independent designers, a marketplace of printable blueprints, and a new economy of custom products. Just like the Internet and MP3’s have freed musical talent from control of big labels, so can widespread RP (Rapid Prototyping) divorce technological innovation from the control of big corporations. (retrieved 23 June 2009)}} | |||
In a similar way IFTF, in the [http://iftf.org/node/1766 Future of Making Map] argues: {{quotationbox|Two future forces, one mostly social, one mostly technological, are intersecting to transform how goods, services, and experiences—the “stuff” of our world—will be designed, manufactured, and distributed over the next decade. An emerging do-it-yourself culture of “makers” is boldly voiding warranties to tweak, hack, and customize the products they buy. And what they can’t purchase, they build from scratch. Meanwhile, flexible manufacturing technologies on the horizon will change fabrication from massive and centralized to lightweight and ad hoc. These trends sit atop a platform of grassroots economics—new market structures developing online that embody a shift from stores and sales to communities and connections. (retrieved 23 June 2009)}} | |||
'''Hands-on future''' is a word play that summarized the idea that is now spreading on the Internet and in venues such as the [http://www.liftconference.com/lift-france-09 LIFT France '09] conference. According to [http://liftlab.com/think/laurent/2009/03/23/hands-on-future/ Laurent Haug], {{quotationbox|What happened in the software industry - young guys waking up with an idea, ending up changing the world from their sofa like it happened with Google, Amazon, Facebook, etc. - is now happening in the tangible world. Things like Arduino are enabling hackers and creators all around the globe, and what was possible with software (easily assemble code to create new applications) is now possible with objects. | |||
The conference program was centered around three main topics: | |||
* Changing Things: Towards objects that are not just “smart” and connected, but also customizable, hackable, transformable, fully recyclable… Towards decentralized and multipurpose manufacturing, or even home fabrication… | |||
* Changing Innovation: Towards continuous and networked innovation, emerging from users as well as entrepreneurs, from researchers as well as activists… | |||
* Changing the Planet: Towards a “green design” that reconnects global environmental challenges with growth, but also with human desire, pleasure, beauty and fun ... }} | |||
The '''Fab Lab''' concept emerged at MIT under the direction of N. Gershenfeld. It included a [[laser cutter]], a miniature milling machine and jigsaw cutting machine. At the same time, people started thinking about creating cheap 3D printers. | |||
The Fab Lab movement also is anchored in ecological thinking. {{quotation|Think of RepRap as a China on your desktop}} (Chris di Bona). Typical materials used in desktop fabrication are not much polluting and there is no transportation cost. The technology will also allow to produce cheap goods that are locally adapted. Finaly, designs can be shared for free, which means that "fab labs" rely on [[open content]], both for the design of the tools and the designs that these tools then can "print". | |||
A possible future was described by Vilbrandt et al (2008) as ''Universal Desktop Fabrication''. {{quotation|Advances in digital design and fabrication technologies are leading toward single fabrication systems capable of producing almost any complete functional object. We are proposing a new paradigm for manufacturing, which we call Universal Desktop Fabrication (UDF), and a framework for its development. UDF will be a coherent system of volumetric digital design software able to handle infinite complexity at any spatial resolution and compact, automated, multi-material digital fabrication hardware. This system aims to be inexpensive, simple, safe and intuitive to operate, open to user modification and experimentation, and capable of rapidly manufacturing almost any arbitrary, complete, high-quality, functional object. Through the broad accessibility and generality of digital technology, UDF will enable vastly more individuals to become innovators of technology, and will catalyze a shift from specialized mass production and global transportation of products to personal customization and point-of-use manufacturing. Likewise, the inherent accuracy and speed of digital computation will allow processes that significantly surpass the practical complexity of the current design and manufacturing systems. This transformation of manufacturing will allow for entirely new classes of human-made, peer-produced, micro-engineered objects, resulting in more dynamic and natural interactions with the world.}} ([http://www.springerlink.com/content/23k0072182021620/?p=e1bfbcc3e9ab4153ab364d31bf57330c&pi=10 Abstract], retrieved 17:30, 25 June 2009 (UTC)). | |||
In October 2008, Evan Malone, the principal designer and implementor of Fab@Home, posted a (draft) [http://nextfab.org/files/draft-functional-block-diagram-futurefab-system Functional Block Diagram for FutureFab System] at NextFab and that is shown below. | |||
[[image:SFF_System_Process_Block_Diagram 2_1.jpg|thumb|800px|none|Functional Block Diagram for FutureFab System by Evan Malone (2008)]] | |||
This diagram shows the complexity of software and hardware constraints interaction. Current '''fabbers''' can't produce "anything", but near future systems will be able to integrate both solid freeform fabrication (printing 3D objects) and electronic components | |||
== History == | == History == | ||
An excellent source for the early history of 3-D models is [http://ccsl.mae.cornell.edu/papers/JMD05_Lipson.pdf Lipson et al, 2004]). According to this paper, {{quotation|Physical models of machines have played an important role in the history of engineering for teaching, modeling, and exploring mechanical concepts. Many of these models have been replaced by computational representations, but new rapid-prototyping technology allows reintroduction of physical models as an intuitive way to demonstrate mechanical concepts}} (Lipson et al, 2004:1032). | |||
Here are a few milestones (that should be completed): | |||
; 15th century | |||
: Filippo Brunelleschi 1377–1436, the architect and engineer of the Duomo in Florence is known to have created construction models. | |||
; 19th century | |||
: Robert Willis (1800–1875) of Cambridge was known for his kinematic teaching models. | |||
: Franz Reuleaux (1829–1905) created the world’s largest collection of kinematic models at the Technical University of Berlin with over 800 models. | |||
; 1940's | ; 1940's | ||
: Birth of [http://en.wikipedia.org/wiki/CNC numerical control], i.e. machine tools controlled by code. | : Birth of [http://en.wikipedia.org/wiki/CNC numerical control], i.e. machine tools controlled by code. | ||
Line 21: | Line 66: | ||
; end 1950's - mid 1960's | ; end 1950's - mid 1960's | ||
: Birth of interfaces of [[Computer- | : Birth of interfaces of [[Computer-aided design]] (CAD) with CNC. | ||
; 1970 | ; 1970 | ||
: | : Mohamed Hashish created a technique to add abrasives to the water jet cutter | ||
; 1986 | |||
: Emergence of 3D-Printing | |||
; 2005 | ; 2005 | ||
: Neil Gershenfeld's et al. MIT class [http://fab.cba.mit.edu/classes/MIT/863.04/ 863.04 - how to make (almost) anything]. | : Neil Gershenfeld's et al. MIT class [http://fab.cba.mit.edu/classes/MIT/863.04/ 863.04 - how to make (almost) anything]. | ||
; 2006 | |||
: The RepRap prototype | |||
; 2007 | ; 2007 | ||
: Neil Gershenfeld and Joe Jacobson MIT class [http://fab.cba.mit.edu/classes/MIT/960.07/ How To Make Something That Makes (almost) Anything]. | : Neil Gershenfeld and Joe Jacobson MIT class [http://fab.cba.mit.edu/classes/MIT/960.07/ How To Make Something That Makes (almost) Anything]. | ||
== | ; 2008 | ||
: First partial DY 3D printer kits | |||
; 2009 | |||
: First complete DYI 3D printer kits, e.g. the [[RapMan]] V3.1 | |||
; 2011 | |||
: A large number of full, small and mini fablabs in the World (about a 100 are listed in [http://wiki.fablab.is/w/index.php?title=Portal:Labs the fablab wiki] | |||
; 2012 | |||
: [[3D printing|3D printers]] become consumer appliances | |||
== Hardware tools == | |||
There exist several popular fab lab technologies, some of which are described below in more details. Most fall in the category of [http://en.wikipedia.org/wiki/Solid_freeform_fabrication solid freeform fabrication] tools and that include: | |||
* [[3D printing|3D printer]]s | |||
* [[Laser cutter]]s | |||
* CNC machines | |||
* Automated paper cutters | |||
* 3D Scanners (for replication) | |||
* Laser sintering | |||
* [[embedded systems building blocks]]: Another kind of toolkits are electronics platforms like [http://www.arduino.cc/ Arduino]. | |||
A '''fabber''' (or '''digital fabricator''') refers to a "factory in box" (i.e. one of the above tools) that can create things automatically from digital data. The [http://www.ennex.com/~fabbers/intro.asp Digital Fabrication Portal] distinguishes three fundamental kinds of fabbers, according to the way they operate on their raw material: | |||
{{quotationbox| | |||
* Subtractive: Material is carved away from a solid block, such as by milling, turning, or electrodischarge machining (EDM). Subtractive fabbers have been automated since the late 1940s, and are often called computer-numerically controlled (CNC) machines. | |||
* Additive: Material is successively added into place to build up the desired object. The methods used include selective curing, selective sintering, and aimed deposition. The first commercial additive fabber was introduced in 1987. * Formative: Material is neither added nor removed, but opposing pressures are applied to the material to modify its shape. Techniques in this category, including automated bending and reconfigurable molding, are under development. | |||
* Hybrid: Processes from two or more of the above categories are combined. Sheet-based fabbers, which cut and laminate successive layers of sheet material, are hybrid subtractive/additive devices. A combination CNC punch press and press brake is a hybrid subtractive/formative fabber. (retrieved 17:25, 24 June 2009 (UTC)).}} | |||
[[image:opensource-washing-machine.jpg|thumb|200px|right|"Open-Source Washing Machine" project]] | |||
As of May 2009, there seemed to be three kinds of ''fab labs'' | |||
* Fairly expensive setups (USD 60K range) that focus a lot on electronics and a large tool set for working with materials. A typical example would be MIT's "FabCentral" Lab described in the [http://fab.cba.mit.edu/about/fab/inv.html Fab Lab inventory]. An other big fab lab, the [http://fablab.waag.org/machines Waag Society] (NL) includes a laser cutter, a milling machine, a Modela milling and scanning machine. a vinyl cutter, an lock stich machine and an embroidery machine. One June 2009, Waag [http://fablab.waag.org/content/fablab-network-worldwide listed about 30 labs] of this type world-wide. | |||
* Small setups that only have 2-3 machines, e.g. a simple 3D desktop printer. Since we expect these [[3D printing|3D printers]] to become cheaper and cheaper, other devices such as [[laser cutter]]s also may become more affordable and therefore popular. Hobby mills are already cheap. | |||
* "Other", e.g. third-world, hobbyist and artist labs who assemble things from various parts, e.g. an [http://www.liftconference.com/news/open-source-washing-machine-liftfrance-09-experience-presentation open source washing machine] from bicycle parts, bamboo, a solar panel and a motor. | |||
As of April 2019, there is more diversity: | |||
* The fabfoundation lists a [http://www.fabfoundation.org/index.php/the-hardware-and-software/index.html The Hardware and Software configuation] for over $110K. Add an extra 50% for Europe to that. A good and safe laser cutter along can cost over 50K. | |||
* Higher education institutions offer a reduced version of this, some some, e.g. the [http://fabricarium.polytech-lille.fr/ fabricarium] (Lille university) come close. | |||
* Some fablabs work with cheap technology, that is refurbished/adapted by engineers, e.g. a laser cutter can be bought for a 1/4 of the price, iff someone is capable of changing/adapting the electronics and software. | |||
* Smaller fablabs, institutionally supported or not often are small spaces that may include only 3D printers, vinyl cutters and small engraving machines. | |||
* Some are specialized, e.g. extensions of existing science or woodcrafts workshop. | |||
* Some are portable (e.g. a big suitcase) or Buses. | |||
* Some are techshops, e.g. more expensive professional prototyping and custom fabrication environments, e.g. the [https://www.techshoplm.fr/ the techshops of LeroyMerlin] in France. The USA "techshops" went broke. | |||
* ... | |||
We found it quite interesting that when wrote the version of this piece in 2009, the MIT and the Waag fab lab did not include 3D-printers in the description of their setup. That probably meant that these two communities lived on two different "planets". However, as of 2011, the "official" list of fab lab engines include a 3D printer. | |||
=== Solid Freeform Fabrication overview === | |||
{{quotation|Freeform Fabrication is a collection of manufacturing technologies with which parts can be created without the need for part-specific tooling. A computerized model of the part is designed. It is sliced computationally, and layer information is sent to a fabricator that reproduces the layer in a real material}} ([http://utwired.engr.utexas.edu/lff/ Laboratory of Freeform Fabrication], UTexas, retrieved 17:25, 24 June 2009 (UTC)). CreatItReal shows an [http://createitreal.com/pages/tech.html animation] of this principle. Typical commercial free form fabricators range between 20'000 and 300'000 $US although low-end 3D printers start at $5000 (June 2009). Open source kits are much cheaper if self-assembled (see [[3D printing]]) | |||
{{quotation| | [[image:reprap-v2extruder.jpg|thumb|400px|right|RepRap Thermoplast Extruder Version 2]] | ||
Low End Solid Freeform Fabrication tools, also called '''rapid prototype machines''' are usually a kind of '''3D printers'''. {{quotation|3D printing is a unique form of fabrication that is related to traditional rapid prototyping technology. A three dimensional object is created by layering and connecting successive cross sections of material. 3D printers are generally faster, more affordable and easier to use than other additive fabrication technologies. While prototyping dominates current uses, 3D printers offers tremendous potential for retail consumer uses.}} ([http://en.wikipedia.org/wiki/3D_printing Wikipedia], retrieved 17:25, 24 June 2009 (UTC)). | |||
Currently, low-end commercial 3D prototypers are becoming affordable for individuals who want to "play" or schools. On oct 2011, the cheapest 3D printer we found was at $2700 from Up! Open source systems cost much less (not counting assembly time) and assembled versions cost about $4000. | |||
Very low-cost non- | According to [http://en.wikipedia.org/wiki/RepRap_Project Wikipedia] (retrieved 17:25, 24 June 2009), {{quotation|Prototypes made by low-end commercial machines cost around US$2 per cubic centimeter to fabricate. The RepRap Project is on track to produce a 3D prototyping machine and free and open source accompanying software that costs about US$400 to build and which can fabricate objects at a cost of about US$0.02 per cubic centimeter.}} | ||
There exist various kinds of 3D printers, e.g. Inkjet-like where layers of powder (e.g. plaster, corn starch or resins) are selectively bonded or photopolymer machines that fix liquids with an UV flood lamp. | |||
* Some low-cost fabbers (e.g. RepRaps) include a kind of "gun" that heats up polymer plastic from a filament and then extrudes a fine stream to build things. | |||
* Another low-cost faber (Fab@Home) uses syringes that you can fill in with Epoxy or some kinds of food. Materials are pushed down by a piston. The Epoxy comes with a resin and a hardener that have to be mixed before filling up the syringe. Malone and Lipson (2007) describe in good detail the architecture of the Fab@Home solid freeform printer. | |||
A similar more complex procedure is called '''fused deposition modeling (FDM)''' (Montaro, 2002) and is described more precisely by Lipson et al. (2004:1030): {{quotation|The process creates a sequence of thermoplastic layers from a filament wound coil that is heated and extruded through a nozzle. The trajectory of the nozzle is derived from the triangle mesh, so as to raster scan and fill solid volumes. In order to create functioning mechanisms, a second, soluble release material is placed in the gaps between the movable parts.}} | |||
=== Low cost 3D Printers === | |||
This article present 3D printing at its beginning in the early 2000's. Also see [[3D printing]] for a more up-to-date article. | |||
[[image:fab-at-home-fabber.jpg|thumb|400px|right|Fab@Home Fabber model 1, 2007: Source [http://www.fabathome.org/wiki/index.php?title=Image:IMG_0110.jpg fabathome.org] ]] | |||
Very low-cost '''non-proprietary 3D printers''' are often referred to as '''Fabbers''' (although the term includes other technologies, including high-end ones). There exist several projects with a high profile in the "web 2.0 sphere". Most printers use a "hot gun" plastic extruder, but other techniques are emerging, e.g. sugar sintering in the CandyFab project. | |||
The [http://www.fabathome.org/ Fab@Home] project (retrieved June 2009) {{quotation|is a project dedicated to making and using ''fabbers'' - machines that can make almost anything, right on your desktop. [...] Fabbers (a.k.a. 3D printers or rapid prototyping machines) are a relatively new form of manufacturing that builds 3D objects by carefully depositing materials drop by drop, layer by layer. With the right set of materials and a geometric blueprint, you can fabricate complex objects that would normally take special resources, tools and skills if produced using conventional manufacturing techniques. A fabber can allow you to explore new designs, email physical objects to other fabber owners, and most importantly - set your ideas free. Just as MP3s, iPods and the Internet have freed musical talent, we hope that blueprints and fabbers will democratize innovation.}}. Fab@Home was conceived by [http://www.mae.cornell.edu/lipson Hod Lipson] of Cornell University and designed and implemented by [http://www.people.cornell.edu/pages/em224 Evan Malone]. Current development includes more people. | |||
[[image:reprap.jpg|thumb|400px|right|RepRap self-replicating 3D printer]] | [[image:reprap.jpg|thumb|400px|right|RepRap self-replicating 3D printer]] | ||
[http://reprap.org/ RepRap] is another well | [http://reprap.org/ RepRap] is another well known project. {{quotation|RepRap is short for Replicating Rapid-prototyper. It is the practical self-copying 3D printer shown on the right - a self-replicating machine. This 3D printer builds the parts up in layers of plastic. This technology already exists, but the cheapest commercial machine would cost you about €30,000. And it isn't even designed so that it can make itself. So what the RepRap team are doing is to develop and to give away the designs for a much cheaper machine with the novel capability of being able to self-copy (material costs are about €500). That way it's accessible to small communities in the developing world as well as individuals in the developed world. Following the principles of the Free Software Movement we are distributing the RepRap machine at no cost to everyone under the GNU General Public Licence. So, if you have a RepRap machine, you can use it to make another and give that one to a friend...}} ([http://reprap.org/bin/view/Main/WebHome What is RepRap?], retrieved 17:25, 24 June 2009 (UTC)). | ||
Until recently, fabbers had to be assembled by the end-user using open designs and low-level parts, i.e. many many days of bricolage. However, some fabbers now can be bought commercially as easy kits or fully assembled. E.g. in ''June 2009'', the [http://store02.prostores.com/servlet/kobask8/StoreFront NextFab Store] sold kits for about $3000 and assembled Fab@Homes for about $4000. [http://www.bitsfrombytes.com/ Bits from Byte] sold a | This RepRap 3D printer builds the parts up in layers of plastic with the help of a custom-made [http://reprap.org/bin/view/Main/ThermoplastExtruder_2_0 Thermoplast Extruder]. Version 2 {{quotation|takes a 3mm diameter filament of a polymer (the single white rod coming into the picture from the top, not to be confused with the pair of white 12V supply wires), forces it down a heated barrel, and then extrudes it as a melt out of a fine nozzle. The resulting thin stream is laid down in layers to form the parts that RepRap makes. The extruder should work up to a temperature of 250o Celsius}}. It works with [http://reprap.org/bin/view/Main/ABS ABS] (Lego-like plastic) and polylactic acid. ([http://reprap.org/bin/view/Main/ThermoplastExtruder_2_0 Thermoplast Extruder Version 2.0], retrieved 17:30, 25 June 2009 (UTC)). In the UK, a RepRap assembly kit with everything included, is available as [[RapMan]] (2009/2010). | ||
The [http://reprap.org/bin/view/Main/MakeYourOwnRepRap next version] of RepRap ([http://reprap.org/bin/view/Main/RepRapTwoMendel RepRap Version 2.0 "Mendel"]) had ambitious plans: {{quotation|will have multiple write heads for working with a wide range of materials in a single reprapped object, and will have the ability to embed three-dimensional electrical circuitry inside mechanical parts. Mendel is still very much in the early stages of development, but the build instructions are themselves under construction at that link.}} | |||
[[image:candyfab-sugarobjects.jpg|thumb|400px|right|CandyFab pure sugar objects]] | |||
The [http://www.candyfab.org/ CandyFab] project is a 3D freeform fabrication project that works with sintering of sugar and other low-melting point materials. This project is different from Fab@Home and RepRap in two ways. The fabricator can print a much larger printable volume but with a lower resolution and you may eat the product. The creators argue that {{quotation|Sugar is a particularly good medium because it's easy to obtain, low in cost, kid friendly, water soluble, non-hazardous, non-toxic, non-intimidating, rigid despite having a low melting point, and may be suitable for making objects for lost sugar (like lost wax) investment casting. We also think that it may also be possible to make interesting food with this technology.}} ([http://www.evilmadscientist.com/article.php/3printerpreview Sneak preview: The Evil Mad Scientist 3D Printer Project], retrieved 17:30, 25 June 2009 (UTC)). | |||
One interesting application of the CandyFab would be to create 3D models of statistical data to be shown in presentations (e.g. a workshop or a thesis defense). After discussion, participants could eat the research results and further discuss data quality and distribution. | |||
[http://www.evilmadscientist.com/article.php/candyfab W.H. Oskay] summarizes the procedure as follows: {{quotation|When the first layer is started, there is a bed of granulated sugar. The heat gun locally melts the top surface of the bed in one point, melting the sugar at that point. The heat gun then moves to the next point, melting the sugar there. If this is done in a number of points in a row, it begins to fill in a line of melted sugar [...]. The sugar only stays molten for about 15-30 seconds after the heat gun is removed from a point. If a second line of melted sugar is added next to the first, you can begin to fill in an area with a thin layer of fused sugar. Let's suppose that you were making a cylinder-- then the first layer would just be a circle. The depth of the melt layer is controlled by the temperature, air flow rate, and hold time at each pixel location. After the first layer is finished, the bed is lowered slightly-- by an amount equal to the melt depth-- and a fresh layer of sugar is added to the top, such that the new top surface is at the same place where the original surface was. To make the next step in the cylinder, a new circle is drawn in the sugar on this layer. For each point in the circle, as the sugar in the top layer melts, it fuses to the corresponding point in the hardened sugar circle below. If we were to let the model cool and take it out of the machine at this point, you would have a solid thin disk, twice the thickness of the melt layer.}} | |||
Until recently, ''Solid Freeform'' fabbers had to be assembled by the end-user using open designs and low-level parts, i.e. many many days of bricolage. However, some fabbers now can be bought commercially as easy kits or fully assembled. E.g. in ''June 2009'', the [http://store02.prostores.com/servlet/kobask8/StoreFront NextFab Store] sold kits for about $3000 and assembled Fab@Homes for about $4000. [http://www.bitsfrombytes.com/ Bits from Byte] sold a (unassembled) [http://www.bitsfrombytes.com/index.php?option=com_content&view=article&id=77&Itemid=100006 RepRap kit] (Version 3 - [[RapMan]]) for about £750. Read the [[RapMan]] entry for additional information. On June 2009, [http://www.makerbot.com/ Cupcake] from MakerBot Industries sold for £750 (unassembled). [http://ccsl.mae.cornell.edu/papers/RPJ07_Malone.pdf Malone and Lipson] (2007) published an interesting breakdown of the cost of the model 1 fab@home 3D printer. Part costs were about $2300 USD plus about 18 hours of assembly work. | |||
[[image:fab-at-home-cost-breakdown.jpg|thumb|600px|none|Fab@Home Model 1 cost breakdown in 2007]] | |||
Within just three years, 3D printing became increasingly popular and as of 2011, several end-user machines are available. Prices started dropping a lot, i.e. commercial kits can be had for $1000 or less as you can see in the [[3D printing]] article. | |||
There also exists a low-cost Laminated Object Manufacturing engines that works with paper. Such a printer can use standard sheets of printer paper and will deposits in a pattern determined by the design. Another sheet of paper is added, and a blade then cuts away the excess paper. Such systems however, were too expensive (e.g. the Matrix 3D may sell for about $20'000). | |||
=== Cutters === | === Cutters === | ||
; | ; Cutters / plotters | ||
[[image:silhouette-cameo.gif|thumb|200px|right|Silhouette Cameo Vinyl cutter]] | |||
: Use a small blade to cut paper, cardstock, vinyl, fabrics etc. They can be bought for as little as $300. E.g. see the list in Bart Bakker's [http://minifablab.nl/index.php?page=vinyl-cutter-plotter Vinyl cutter / plotter] page. A popular entry-level model is the [[Silhouette Cameo]]. | |||
; Laser cutters and engravers | |||
: Laser cutters and engravers can process any non-metal material (e.g. acrylic, ceramics, cork, fiberglass, glass, plastic, leather, paper, stone, wood). {{quotation|Laser cutting is a technology that uses a laser to cut materials, which is used in the production line and is typically used for industrial manufacturing applications. Laser cutting works by directing the output of a high power laser, by computer, at the material to be cut. The material then either melts, burns, vaporizes away, or is blown away by a jet of gas, [1] leaving an edge with a high quality surface finish. Industrial laser cutters are used to cut flat-sheet material as well as structural and piping materials.}} ([http://en.wikipedia.org/wiki/Laser_cutting Wikipedia], retrieved 17:25, 24 June 2009 (UTC)). | |||
According to [http://www.fablab.nl/articles/2011/01/03/mini-fablab Bart Bakker] (oral communication, dec 2011), [[Laser cutter]]s are the most popular tools in Netherland's fablabs. Laser cutters can't be used in closed rooms (i.e. needing air filtering). They also are expensive, although some exciting developments are out there, in particular [http://www.laoslaser.org/ LAOS], i.e. an open source replacement board and software that could be use to drive cheap chinese hardware. | |||
; Laminated Object Manufacturing (LOM) | |||
: {{quotation|Laminated object manufacturing (LOM) is a rapid prototyping system developed by Helisys Inc. (Cubic Technologies is now the successor organization of Helisys) In it, layers of adhesive-coated paper, plastic, or metal laminates are successively glued together and cut to shape with a knife or a laser cutter.}} ([http://en.wikipedia.org/wiki/Laminated_object_manufacturing Wikipedia], retrieved 17:30, 25 June 2009 (UTC)) | |||
; Plasma cutters | ; Plasma cutters | ||
: {{quotation|Plasma cutting is a process that is used to cut steel and other metals of different thicknesses (or sometimes other materials) using a plasma torch. In this process, an inert gas (in some units, compressed air) is blown at high speed out of a nozzle; at the same time an electrical arc is formed through that gas from the nozzle to the surface being cut, turning some of that gas to plasma. The plasma is sufficiently hot to melt the metal being cut and moves sufficiently fast to blow molten metal away from the cut. Plasma can also be used for plasma arc welding and other applications.}} ([http://en.wikipedia.org/wiki/Plasma_cutting Wikipedia], retrieved 17:25, 24 June 2009 (UTC)). | |||
Plasma cutters come in various sizes and are available from $3000. | |||
; Water jet cutter | ; Water jet cutter | ||
Line 60: | Line 199: | ||
According to [http://en.wikipedia.org/wiki/Water_jet_cutter Wikipedia], | According to [http://en.wikipedia.org/wiki/Water_jet_cutter Wikipedia], | ||
water jets can cut with a with of about 1mm and can cut materials such as rubber, foam, plastics, composites, stone, | water jets can cut with a with of about 1mm and can cut materials such as rubber, foam, plastics, composites, stone, glass, tile, metals, food, paper and much more. Also, water jets can cut material without much harming or changing the materials' structures since there is no heat. I also can be considered a green technology, since it doesn't produce harmful waste. Water and abrasives can be recycled. | ||
[[image:lumemlab-micro.jpg|frame|right|none|Lumenlab's micRo-CNC ($599 if you assemble it yourself)]] | |||
; Shopbots | |||
: Computer-controlled ShopBots are do-all tool for precisely cutting, carving, drilling or machining all kinds of things from all kinds of materials. {{quotation|A ShopBot is like a large plotter that moves pens around the surface (in X and Y axes) to create a drawing. Only a ShopBot moves a cutter around a big table (X and Y axes) and moves it up and down as well (Z axis) allowing it to make 3D movements and cut all sorts of shapes. The cutter looks like a drill bit and is spun by a motor called a router or spindle. Unlike a drill bit, a router bit is designed to cut from the sides as well as the tip. By precisely moving the cutter through material, a ShopBot CNC tool can create virtually any pattern or shape and will do it in materials such as wood, plastic, foam, aluminum and many composites.}} ([http://www.shopbottools.com/WhatsCNC.htm What's All the Excitement About ShopBot CNC Tools?], retrieved 17:30, 25 June 2009 (UTC)). Prices start at $7500. | |||
; Combined mill / cutter / printer | |||
Various technology can be combined into 3-axis CNC robots. As an example: {{quotation|[https://www.lumenlab.com/ micRo] is a unique system which can be used for both additive (printing) and subtractive (milling, cutting) fabrication. It is a precise, modular tool which allows you to create complex objects out of wood, metal, plastic and more}} | |||
[[image:solarsiter018.jpg|thumb|300px|right|Markus Kaiser's [http://www.markuskayser.com/work/solarsinter/ SolarSinter], a cool low/high tech version]] | |||
=== Selective Laser sintering === | |||
{{quotation|In the Selective Laser Sintering (SLS) process, three-dimensional parts are created by fusing (or sintering) powdered thermoplastic materials with the heat from an infrared laser beam.}} ([http://www.protocam.com/html/sls.html Selective Laser Sintering (SLS), SLS Prototype], retrieved 17:25, 24 June 2009 (UTC)). | |||
:{{quotation|Selective laser sintering is an additive rapid manufacturing technique that uses a high power LASER (for example, a carbon dioxide laser) to fuse small particles of plastic, metal, ceramic, or glass powders into a mass representing a desired 3-dimensional object. The laser selectively fuses powdered material by scanning cross-sections generated from a 3-D digital description of the part}} ([http://en.wikipedia.org/wiki/Selective_laser_sintering Wikipedia], retrieved 17:25, 24 June 2009 (UTC)). | |||
This technology if fairly complex and expensive compared to low-end 3D printers that extrude plastic. However, Markus Kayser in his [http://www.markuskayser.com/work/solarsinter/ SolarSinter] demoed a cool bricolage version that sinters sand with solar energy. Also, commercial laser sintering printers should probably soon be available for less than 10K. (dec/2011). | |||
=== Stereolithography (SLA) === | |||
Stereolithography (or photopolymerization) {{quotation|is a common rapid manufacturing and rapid prototyping technology for producing parts with high accuracy and good surface finish. A device that performs stereolithography is called an SLA or Stereolithography Apparatus.}} ([http://en.wikipedia.org/wiki/Stereolithography Wikipedia], retrieved 17:25, 24 June 2009 (UTC)). | |||
SLA is too expensive for fab labs (between $100,000 and $400,000) | |||
=== CNC mills === | === CNC mills === | ||
Line 66: | Line 230: | ||
A milling machine (fr. "fraiseuse") is a machine tool used for the shaping of metal and other solid materials. It uses rotating cutters to cut stuff from a workpiece. In more sophisticated milling machines, both the cutters and the workpiece can be rotated in three axis. | A milling machine (fr. "fraiseuse") is a machine tool used for the shaping of metal and other solid materials. It uses rotating cutters to cut stuff from a workpiece. In more sophisticated milling machines, both the cutters and the workpiece can be rotated in three axis. | ||
=== CNC Hobby Mills === | |||
See also: | |||
* [[hobby milling]] | |||
* Shopbots above | |||
[[image:iModela_dgj009.jpg|thumb|250px|right|Roland iModela Hobby Mill]] | |||
A whole variety of hobby mills are now available and work with softer materials, e.g. the [http://www.rolanddg.com/news/nr111005_im-01.html Roland iModela iM-01 Hobby Mill]. According to [http://www.rolanddg.com/news/nr111005_im-01.html the product announcement page], retrieved 14:33, 7 December 2011 (CET), the iModela is an inexpensive (about $1000), easy-to-use desktop device that mills wax, foam, balsa wood and plastic materials commonly used in craft and hobby projects. The [http://icreate.rolanddg.com/ iCreate] web site includes a few sample designs plus other support materials. This model can read IGES, DXF and STL and only works with Windows. | |||
=== Computer controlled embroidery machines === | |||
A [[computerized embroidery|computer-controlled embroidery machine]] allows to print out complex designs, e.g. embroidery. | |||
=== 3D Scanners === | |||
An alternative to designing objects is to scan them. | |||
Rotating 3D scanners can be bought for about $3000, but hand-held Laser 3D scanning costs next to nothing (see the links section below for pointers). | |||
=== Electronic kits === | |||
See also: [[Embedded systems building blocks]], often that kind of hardware is specially made for education. | |||
; Arduino | |||
[http://www.arduino.cc/ Arduino] {{quotation|is an open-source electronics prototyping platform based on flexible, easy-to-use hardware and software. It's intended for artists, designers, hobbyists, and anyone interested in creating interactive objects or environments.<br/> | |||
Arduino can sense the environment by receiving input from a variety of sensors and can affect its surroundings by controlling lights, motors, and other actuators. The microcontroller on the board is programmed using the Arduino programming language (based on Wiring) and the Arduino development environment (based on Processing). Arduino projects can be stand-alone or they can communicate with software on running on a computer (e.g. Flash, Processing, MaxMSP).}} ([http://www.arduino.cc/ Arduino Home Page], retrieved 17:25, 24 June 2009 (UTC)). | |||
; OpenMoko | |||
[http://wiki.openmoko.org/ OpenMoko] is is a project dedicated to delivering mobile phones with an open source software stack. Openmoko is currently (June 2009) selling the Neo FreeRunner phone to advanced users and will start selling it to the general public as soon as the software is more developed. | |||
{{quotation|The Openmoko stack, which includes a full X server, allows users and developers to transform mobile hardware platforms into unique products. Our license gives developers and users freedom to cosmetically customize their device or radically remix it; change the wallpaper or rebuild the entire house! It grants them the freedom, for example, to transform a phone into a medical device or point of sale device or the freedom to simply install their own favorite software. Beyond freeing the software on our devices we have also released our CAD files. And at LinuxWorld 2008, we announced the release of the schematics for our products.}} ([http://wiki.openmoko.org/wiki/Introduction Introduction], retrieved 17:30, 25 June 2009 (UTC)). | |||
; The Make controller kit | |||
The [http://www.makingthings.com/store/make-controller/make-controller-kit.html Make Controller Kit] sponsored by [http://www.makezine.com/ Make magazine], is an open source hardware solution for hobbyists and professionals to create interactive applications. It supports desktop interfaces via a variety of languages such as Max/MSP, Flash, Processing, Java, Python, Ruby, or anything that supports Open Sound Control (OSC). | |||
== Software == | |||
See | |||
* [[Computer-aided design and manufacturing]] (CAD/CAM) | |||
* [[3D printing]] | |||
* [[Computerized embroidery]] | |||
== Links == | == Links == | ||
=== Fab | === Fab Lab portals and overviews === | ||
* [http://fab.cba.mit.edu/ FabCentral], The Center for Bits and Atoms, MIT. | * [http://fab.cba.mit.edu/ FabCentral], The Center for Bits and Atoms, MIT. Inventor of FabLab classes. | ||
** [http://fab.cba.mit.edu/about/faq/ Fab Lab FAQ], MIT. (includes further pointers). | ** [http://fab.cba.mit.edu/about/faq/ Fab Lab FAQ], MIT. (includes further pointers). | ||
** [http://fab.cba.mit.edu/classes/MIT/863.08/people/alex_schaub/ How to make (almost) anything] (alex schaub's mas863 log Fall 2008). Illustrates what could be done. | |||
* [http://fablabatschool.org/ The
FabLab@School], created by Prof. Paulo Blikstein at Stanford University is a new type of digital fabrication lab especially designed for schools and children, with several special characteristics. | |||
* [http://www.media.mit.edu/research/groups/high-low-tech High-Low Tech] group (MIT Media Lab). Explore the intersection of computation, physical materials, manufacturing processes, traditional crafts, and design. | |||
; Wikipedia articles | |||
* [http://en.wikipedia.org/wiki/3D_printing Wikipedia] | |||
* [http://en.wikipedia.org/wiki/Category:Solid_freeform_fabrication Category:Solid freeform fabrication] (Wikipedia). | |||
* [http://en.wikipedia.org/wiki/Desktop_manufacturing Desktop manufacturing] (Wikipedia) | |||
* [http://en.wikipedia.org/wiki/Digital_fabricator Digital fabricator] (Wikipedia) | |||
* [http://en.wikipedia.org/wiki/Fabber Fabber] (Wikipedia). | |||
* [http://en.wikipedia.org/wiki/Solid_freeform_fabrication Solid freeform fabrication] (Wikipedia, overview). | |||
; Overviews | |||
* [http://home.att.net/~castleisland/rp_int1.htm The Most Important Commercial Rapid Prototyping Technologies at a Glance] | |||
* [http://seedmagazine.com/content/article/is_mit_obsolete/ On the future of invention], by Neil Gershenfeld, Seedmagazine, June 24, 2009. | |||
* [http://www.economist.com/science/displayStory.cfm?story_id=3786368 Desktop manufacturing - Helping poor-world inventors], The Economist, Mar 23 2005. | * [http://www.economist.com/science/displayStory.cfm?story_id=3786368 Desktop manufacturing - Helping poor-world inventors], The Economist, Mar 23 2005. | ||
* [http://www.ennex.com/~fabbers/intro.asp What is a Fabber?, An Introduction to the 21st Century], Ennex Corporation, retrieved 17:25, 24 June 2009 (UTC). | |||
* [http://www.popularmechanics.com/automotive/jay_leno_garage/4320759.html Jay Leno’s 3D Printer Replaces Rusty Old Parts] | |||
* [http://www.rapidprototypinghomepage.com/ Rapid Prototyping Home Page] | * [http://www.rapidprototypinghomepage.com/ Rapid Prototyping Home Page] | ||
* [http://www.3d-print.in/ 3D Printers and 3D Printing Technology Blog] | |||
* [http:// | * [https://www.nytimes.com/books/first/h/himanen-hacker.html The Hacker Ethic and the Spirit of the Information Age] by Pekka Himanen (book excerpt) | ||
* [http://www.tedxbrussels.eu/2012/speakers/mitch_altman.php Mitch Altman on "The Hackerspace Movement"] (TEDx talk video, Brussels, 2012). | |||
=== Repositories === | |||
; Models (designs in some format that can be "printed") | |||
* [http://new-objects.com/ New objects] (includes visualization and downloadable files) | |||
* [http://3dprintables.org 3dprintables.org] (excellent wiki includes educational objects, often with links models on external sites) | |||
* [http://www.thingiverse.com/ thingiverse] (a place to share digital designs that can be made into real, physical objects). '''Many''' interesting objects for RepRap machines like the [[RapMan]] | |||
* [http://openprosthetics.org/ Open Prosthetics Project] is producing useful innovations in the field of prosthetics and freely sharing the designs | |||
* [https://www.opendesk.cc/ Opendesk] (Furniture) | |||
; How-to | |||
* [http://www.instructables.com/ Instructables] Instructions on how to build various things | |||
; Hardware models | |||
* [http://kmoddl.library.cornell.edu/ KMODDL]. Some open source models are available in the [http://kmoddl.org/ Machines and Mechanisms Wiki] | |||
=== 3D printing === | |||
See [[3D printing]] | |||
=== Numerical control === | === Numerical control === | ||
Line 86: | Line 341: | ||
* [http://en.wikipedia.org/wiki/CNC Numerical control] (Wikipedia) | * [http://en.wikipedia.org/wiki/CNC Numerical control] (Wikipedia) | ||
=== | === Cheap 3D scanning === | ||
[[image:david-laserscan2.jpg|thumb|200px|right| Plush Lion - front scan with David LaserScanner ]] | |||
* [[David Laserscanner]], A complete system with calibration panels, camera, red laser and software is about 350 Euros. But you also can buy just parts, e.g. the 90.- red laser and build the rest yourself. The software includes scanning, interpolation, some editing and shape fusion with various methods. To the right you can see a picture of one scan, i.e. our first attempt using this system - [[User:Daniel K. Schneider|Daniel K. Schneider]] 17:36, 8 December 2009 (UTC) | |||
=== Other Fab Lab hardware === | |||
'''Laser and plasma cutters''' | |||
* [http:// | * [http://home.howstuffworks.com/plasma-cutter.htm How Plasma Cutters Work] (Howstuffworks.com). | ||
* [http://home.att.net/~castleisland/ | * [http://home.att.net/~castleisland/lom_int.htm Laminated Object Manufacturing] and [http://home.att.net/~castleisland/lom.htm Laminated Object Manufacturing] | ||
'''Water jets''' | |||
* [http://www.waterjets.org/ Waterjets.org] | * [http://www.waterjets.org/ Waterjets.org] | ||
* [http://science.howstuffworks.com/question553.htm How Water Jets Work] | * [http://science.howstuffworks.com/question553.htm How Water Jets Work] | ||
'''CNC mills''' | |||
* [http://www.volunteerlabrat.com/default.html?goto=cnc.html The CNC mill project] | * [http://www.volunteerlabrat.com/default.html?goto=cnc.html The CNC mill project] | ||
* [http://www.lumenlab.com/ Lumenlab's lowcost 3D CNC milling/cutting/printing systems] | |||
* [http://lcamtuf.coredump.cx/guerrilla_cnc1.shtml Guerrilla guide to CNC machining and resin casting] '''Good''', detailed tutorial. | |||
'''CNC shopbots''' | |||
* [http://www.shopbottools.com/ Shopbottools.com]. E.g. have a look at the [http://www.shopbottools.com/spotlight.htm portfolio] of projects (including school contexts). Prices are from $7500 to $20K. | |||
'''Selective Laster Sintering (SLS)''' | |||
* [http://home.att.net/~castleisland/sls.htm Selective Laser Sintering] | |||
'''Stereolithography (SLA)''' | |||
* [http://home.att.net/~castleisland/sl.htm Stereolithography (SLA)], Castle Island Co., retrieved 17:25, 24 June 2009 (UTC) | |||
=== Electronics === | |||
In order to avoid hassles with repairs and an such, it is probably a good idea to buy in your own country. E.g. in Switzerland, there is the [http://dshop.ch/ dshop] (an Arduino/OpenMoko vendor) | |||
; Arduino | |||
* [http://www.arduino.cc/ Arduino] (Home page) | |||
* [http://www.youtube.com/results?search_type=&search_query=arduino&aq=f YouTube Videos] | |||
* Most Arduino products are [http://arduino.cc/en/Main/Hardware I/O Boards] on top of which one can insert ''shields'' (extensions). Various parts range from cheap to $400.-. See the [http://arduino.cc/en/Main/Buy vendor page]. Some OpenSource 3D fabbers use these boards. | |||
* There exist many Arduino clones (since the design is open source). See the Wikipedia page. | |||
* [http://en.wikipedia.org/wiki/Arduino Arduino] (Wikipedia). | |||
* [http://spectrum.ieee.org/geek-life/hands-on/the-making-of-arduino/0 The Making of Arduino] IEEE Spectrum, By David Kushner / October 2011 | |||
; OpenMoko | |||
* Openmoko is a project dedicated to delivering mobile phones with an open source software stack. It can run with various OSs, e.g. it got official Debian support and also runs with Android. | |||
* [http://wiki.openmoko.org/ OpenMoko] (Home page) | |||
* [http://www.techtree.com/India/Reviews/Freerunner/551-93139-612.html TechTree review of Freerunner] | |||
* [http://us.direct.openmoko.com/ OpenMoko Store]. The FreeRunner (A6) model is sold for $250. | |||
; Make Controller Kit | |||
[http://www.makingthings.com/store/make-controller/make-controller-kit.html Make Controller Kit] online sales at [http://www.makingthings.com/ Making Things.com] | |||
=== New technology mags, blogs and communities === | |||
(Closely or loosely related to fablabs) | |||
* [http://waag.org/en/project/make-future Make the future] (Waag society/ United Nations Development Programme, UNDP) | |||
* [http://seedmagazine.com/ SEED magazine] | |||
* [http://www.newscientist.com/section/tech NewScientist] (tech section) | * [http://www.newscientist.com/section/tech NewScientist] (tech section) | ||
* [http://fablabs.ning.com/ FabLabs - a space for those tinkering with Fab Labs] | |||
* [http://www.thingiverse.com/ Thingiverse]. Is a place for you to share your digital designs with the world. | |||
* [http://hackedgadgets.com/ Hacked Gadgets] | |||
* [http://www.nycresistor.com/ NYC Resistor] is a hacker collective with a shared space located in downtown Brooklyn. | |||
* [http://nextbigfuture.com/ Next Big Future] (blog) | |||
* [http://liftlab.com/think/nova Pasta&Vinegar], Nicolas Nova, LiftLab (mind/tech bazar from outer space blog). | |||
* [http://www.liftconference.com/ The LIFT conference series] (organized by our friends from LiftLab). | |||
* [http://makezine.com/ Make magazine] (The most popular commercial geeky do it yourself magazine) | |||
* [http://www.makingthings.com/projects MakingThings] (project page) | |||
* [http://www.lowtechmagazine.com/ Low Tech Magazine]. for ideas | |||
* [http://fabstar.org/manchester2012/ Fab ✱ Manchester 2012] (conference) | |||
* [http://tltl.stanford.edu/fablearn2012 FabLearn 2012] | |||
* [http://opensourceecology.org/ OpenSourceEcology.org], high-performance, modular, do-it-yourself, low-cost platform - that allows for the easy fabrication of the 50 different industrial machines that it takes - to build a small, sustainable civilization with modern comforts. | |||
=== Fab Labs === | |||
* [http://fab.cba.mit.edu/ Fab Lab Central] (MIT, USA). Includes pointers to many FabLabs world-wide. | |||
* [http://fablab.waag.org/ Fablab Amsterdam] (Netherlands) | |||
* [http://utwired.engr.utexas.edu/lff/ Laboratory for Freeform Fabrication] (UTexas, USA). | |||
* [http://fablabsquared.org/ FabLab Squared] (France) | |||
* [http://www.minifablab.nl/ miniFABLAB] (Netherlands) | |||
* [http://www.hslu.ch/hochschule-luzern/h-interdsiziplinaere-schwerpunkte/h-is-crealab.htm Creating Living Lab] (Hochschule Luzern, Switzerland) and [http://luzern.fablab.ch/ Fablab] (Luzern) | |||
=== Mobile fablabs === | |||
There exist a number of solutions, i.e. several organizations do have buses that include fablab. | |||
* [https://www.fablab-en-kit.com/ Fablab en kit] offers a big foldable container that can fit into a mini-van. | |||
== Bibliography == | == Bibliography == | ||
See also [[digital design and fabrication bibliography]] and [[fab labs in education]] | |||
* Bereza, Marek (2007). Rise of the Replicator: The Evolution of Media Into The Tangible. The Royal College of Art, ''Master thesis''. [http://www.wikid.co.uk/files/dissertation.pdf PDF] | |||
* Blikstein, Paolo, Sylvia Libow Martinez, and Heather Allen Pang (eds). (2016). Meaningful Making: Projects and Inspirations for Fab Labs + Makerspaces, CONSTRUCTING MODERN KNOWLEDGE PRESS, Print book ISBN: 978-0- 9891511-9-1, e-book ISBN: 978-0- 9891511-2- 2, http://fablearn.stanford.edu/fellows/page/meaningful-making-book. | |||
* Breen, Jack; Robert Nottrot, Martijn Stellingwerff (2003). Tangible virtuality--perceptions of computer-aided and physical modelling, Automation in Construction, Volume 12, Issue 6, Design e-ducation: Connecting the Real and the Virtual, November 2003, Pages 649-653, ISSN 0926-5805, DOI: [http://dx.doi.org/10.1016/S0926-5805(03)00053-0 10.1016/S0926-5805(03)00053-0]. | |||
* Burns M., (1995) The Freedom to Create, in Technology Management, Volume 1, Number 4 http://www.ennex.com/~fabbers/publish/199407-MB-FreedomCreate.asp | * Burns M., (1995) The Freedom to Create, in Technology Management, Volume 1, Number 4 http://www.ennex.com/~fabbers/publish/199407-MB-FreedomCreate.asp | ||
* | * Bowyer, Adrian (2007) Why Accountants are Dull and Guitarists are Glamourous - The End of Intellectual Property, Time Compression Technology Magazine, volume 15, issue 3, p33 (2007). | ||
* Bowyer, Adrian (2007)- The Self-replicating Rapid Prototyper ─ Manufacturing for the Masses, Invited Keynote Address, Proc. 8th National Conference on Rapid Design, Prototyping & Manufacturing, Centre for Rapid Design and Manufacture, High Wycombe, June 2007. Rapid Prototyping and Manufacturing Association, ISBN-13: 978-0948314537 (2007). | |||
* Bowyer, Adrian (2007). Breed your own Design, Icon Magazine, volume 52, October 2007. | |||
* Burry, Mark; Michael Ostwald, Peter Downton, Andrea Mina, (2007) Homo Faber - Modelling Architecture, Sydeney: Archadia Press, ISBN 9780977571123. [http://www.homo-faber.net/hf_2006_catalogue.pdf PDF] (See also the video: [http://www.sial.rmit.edu.au/Projects/Thinking_Modelling_Making.php Thinking modeling making] | |||
* Ceccarelli, M., (Ed.) 2000, International Symposium on History of Machines and Mechanisms, Proc. HMM Kluwer Academic, Dordrecht. | |||
* Cohen D. L., Malone E., Lipson H., Bonassar L., (2006) "3D direct printing of heterogeneous tissue implants", Tissue Engineering, Vol. 12, No. 5: 1325-1335 | |||
* Editors' Review (2005). ''Desktop Factories - FAB The Coming Revolution on Your Desktop -- from Personal Computers to Personal Fabrication By Neil Gershenfeld, Basic Books'', Business Week, May 2 2005. | * Editors' Review (2005). ''Desktop Factories - FAB The Coming Revolution on Your Desktop -- from Personal Computers to Personal Fabrication By Neil Gershenfeld, Basic Books'', Business Week, May 2 2005. | ||
* Evil Mad Scientist Laboratories (2007). Solid freeform fabrication: DIY, on the cheap, and made of pure sugar, http://www.evilmadscientist.com/article.php/candyfab, retrieved 17:30, 25 June 2009 (UTC). | |||
* Flichy, Patrice (2010), Le sacre de l'amateur : Sociologie des passions ordinaires à l'ère numérique, Seuil. | |||
* Gershenfeld N. ''Think Globally, fabricate locally'', PrincipalVoices.com. [http://ng.cba.mit.edu/dist/PV.pdf PDF] (reprint) | * Gershenfeld N. ''Think Globally, fabricate locally'', PrincipalVoices.com. [http://ng.cba.mit.edu/dist/PV.pdf PDF] (reprint) | ||
* Gershenfeld, Neil, A., (2005) FAB: The Coming Revolution on Your Desktop – From Personal Computers to Personal Fabrication, Basic Books, ISBN 0-465-02745-8. | |||
* Institute of the Future (2009). ''The future of making'', [http://iftf.org/system/files/deliverables/SR-1154+TH+2008+Maker+Map.pdf PDF] | |||
* Kuznetsov, Stacey and Eric Paulos (2010). Rise of the Expert Amateur: DIY Projects, Communities, and Cultures, ''Proceedings of ACM NordiCHI 2010: Extending boundaris'', Reykjavik, [http://staceyk.org/hci/KuznetsovDIY.pdf PDF preprint] | |||
* Jenweill, Mark, ''Fab Labs unshackle imaginations'', USA Today, 11/6/2005. | * Jenweill, Mark, ''Fab Labs unshackle imaginations'', USA Today, 11/6/2005. | ||
* | * Moon, F. C., 2003a, Franz Reuleaux: Contributions to 19th Century Kinematics and Theory of Machines, ''Applied Mechanics Reviews'', American Society of Mechanical Engineers, N.Y. | ||
* Lillard, A. and Else-Quest, N. (2006) The Early Years: Evaluating Montessori Education Science, Vol. 313. no. 5795, pp. 1893 - 1894 | |||
* Lipson H., Moon F.C., Hai J., Paventi C., (2004) 3D-Printing the History of Mechanisms, ASME Journal of Mechanical Design, pp. 1029-1033. [http://ccsl.mae.cornell.edu/papers/JMD05_Lipson.pdf PDF] | |||
* Lipson H. (2005a) "Homemade: The future of Functional Rapid Prototyping", IEEE Spectrum, feature article, May 2005, pp. 24-31 http://www.mae.cornell.edu/ccsl/papers/Spectrum05_Lipson.pdf | |||
* Lipson H. (2005b). [http://www.mae.cornell.edu/ccsl/papers/Spectrum05_Lipson.pdf "Homemade: The future of Functional Rapid Prototyping"], IEEE Spectrum, feature article, May 2005, pp. 24-31. | |||
* Lobovsky M., Lobovsky A., Behi M., Lipson H. (2008), "Solid Freeform Fabrication of Stainless Steel Using Fab@Home", Proceedings of the 19th Annual Solid Freeform Fabrication Symposium, Austin TX, Aug 2008. [http://ccsl.mae.cornell.edu/papers/SFF08_Lobovsky.pdf PDF] | |||
* Malone, E. (2006). Faxing Artifacts: The promise of three-dimensional scanning and rapid prototyping of archaeological materials, International Council of Archaeo-Zoologists – ICAZ 2006, Mexico City, Mexico, 23-28 Aug 2006, [http://www.simpleware.com/applications/medical.php Poster]. | |||
* Malone E., Lipson H., (2006) "Freeform Fabrication of Ionomeric Polymer-Metal Composite Actuators", Rapid Prototyping Journal, Vol. 12, No. 5, pp.244-253. | |||
* Malone E., Lipson H., (2007) "Fab@Home: The Personal Desktop Fabricator Kit", Rapid Prototyping Journal, Vol. 13, No. 4, pp.245-255. [http://ccsl.mae.cornell.edu/papers/RPJ07_Malone.pdf PDF]. (This is to our knowledge the best easy to read '''article explaining most aspects of a desktop fabricator'''). | |||
* Malone E., Rasa K., Cohen D. L., Isaacson T., Lashley H., Lipson H., (2004) "Freeform fabrication of 3D zinc-air batteries and functional electro-mechanical assemblies", Rapid Prototyping Journal, Vol. 10, No. 1, pp. 58-69. | |||
* Malone, E., Berry, M., Lipson, H., (2008), "Freeform Fabrication and Characterization of Zinc-air Batteries", Rapid Prototyping Journal, Vol. 14, No. 3, pp. 128-140. [http://www.mae.cornell.edu/ccsl/papers/RPJ08_Malone.pdf PDF] | |||
* Apoorva Mandavilli (2006). Appropriate technology: Make anything, anywhere, Nature 442, 862-864 (24 August 2006). [http://dx.doi.org/doi:10.1038/442862a doi:10.1038/442862a]. | |||
* McMains, S. (2005). [http://portal.acm.org/citation.cfm?id=1064858&coll=ACM&dl=ACM&CFID=13415255&CFTOKEN=78174790 "Layered Manufacturing Technologies"], Comm. ACM, Volume 48, Number 6, pp 50-56. | |||
* Mikhak, Bakhtiar; Christopher Lyon, Tim Gorton, Neil Gershenfeld, Caroline McEnnis and Jason Taylor (unknown). Fab Lab: An Alternate Model Of Ict For Development, [http://cba.media.mit.edu/events/03.05.fablab/fablab-dyd02.pdf PDF] | |||
* Milanese, Fiona (2006). FABLab allows you to create the gadget of your dreams, Science in Africa. August 2006, [http://www.scienceinafrica.co.za/2006/august/fablab.htm HTML] | |||
* Montaro, M. et al., 2002, “Material Characterization of Fused Deposition Modeling (FDM) ABS by Designed Experiments,” University of California, Berkeley Report. | |||
* Sells, Ed; Zach Smith, Sebastien Bailard, and Adrian Bowyer (2007). RepRap: The Replicating Rapid Prototyper - Maximizing Customizability by Breeding the Means of Production. Extended abstract in Proc. Mass Customization and Personalization Conference, MIT, October 2007. | |||
* STEEG, T., 2008. Makers, Hackers and Fabbers: what is the future for D&T? IN: Norman, E.W.L. and Spendlove, D. (eds.). The Design and Technology Association International Research Conference, [Loughborough University, 2-4 July]. Wellesbourne : The Design and Technology Association, pp. 65-73. [https://magpie.lboro.ac.uk/dspace-jspui/bitstream/2134/3492/1/Steeg_Conference 08.pdf PDF] - [https://magpie.lboro.ac.uk/dspace-jspui/handle/2134/3492 HTML Abstract]. (includes throughts about Design and Technology teaching) | |||
* Thomson, Clive (2008). [http://www.wired.com/techbiz/startups/magazine/16-11/ff_openmanufacturing?currentPage=all Build It. Share It. Profit. Can Open Source Hardware Work?] Wired Magazine, 16:1 | |||
* Touchgraphics, Inc. (2009). An Interactive Talking Campus Model at Carroll Center for the Blind, Final Report, [http://touchgraphics.com/downloads/carroll center talking campus model final report low.pdf PDF]. (Objects were created with a commercial 3D printer). | |||
* Vilbrandt, T., Malone, E., Lipson H., Pasko, A., (2008) "Universal Desktop Fabrication", in Heterogeneous Objects Modeling and Applications, pp. 259-284. DOI: [http://dx.doi.org/10.1007/978-3-540-68443-5 10.1007/978-3-540-68443-5] {{ar}} | |||
; Links | |||
* [http://people.bath.ac.uk/ensab/Pubs/all_pubs.html Adrian Bowyer's Publications] | |||
* [http://nextfab.org/content/evan-malone Evan Malone's publications] | |||
* [http://ccsl.mae.cornell.edu/publications Cornell Computational Synthesis Laboratory publications] | |||
* [http://l3d.cs.colorado.edu/~ctg/Pubs.html Craft Technology publications] (University of Colorado, Boulder) | |||
== Acknowledgment == | |||
Thanx to [http://liftlab.com/think/nova Nicolas Nova] for inviting [[User:Daniel K. Schneider|Daniel K. Schneider]] to [http://www.liftconference.com/lift-france-09 LIFT France '09] which gave me the impulse for writing a first version of this piece and to explore various [[:category:Fab lab|sub topics]] in more depth. | |||
[[Category:Hardware]] | [[Category:Hardware]] | ||
[[Category: Fab lab]] | |||
[[Category: Innovation and change]] | |||
[[Category:Design methodologies]] | |||
[[Category: 3D printing]] | |||
[[Category: Computerized embroidery]] | |||
[[Category: Cutting plotter]] |
Latest revision as of 12:11, 14 January 2020
Most parts of this piece have been written in 2011 and 2012 and some may need updating.
Introduction
A Fab Lab or fablab (fabrication laboratory) is a small-scale workshop with computer controlled tools with the aim to make "almost anything". (Wikipedia).
Fab labs are a disruptive technology. In the same way that micro computers changed computing, desktop fabbers (fab lab machines) may change manufacturing, i.e. people can produce things at home or within small organizations.
Fablabs are typically open to the public and should have a charter. Other types of collaborative workshops for making are maker spaces, hacker spaces, tech shops, fac labs, etc. A space with a lone 3D printer should not be called a fablab.
Fab labs and 3D printers in particular will have a certain impact on education including computer-supported educational technology. Examples of educational domains and applications are design teaching (in engineering or design schools), producing constructionist learning objects (manipulatives that may or may not be augmented with computer technology), and creation of replicas or augmented objects for museum learning.
See also:
- Fab labs in education (overview article with links and bibliography)
- Digital design and fabrication bibliography
- Constructionist learning objects and Fröbel gifts, i.e. educational application areas with potential for desktop fabbers.
- Tour de Fablab (under construction until december 2011)
- Fablab TECFA
- 3D printing
- computerized embroidery
- hobby milling
- Vinyl cutting (Silhouette Cameo)
Fab labs can have different aims, e.g. the include rapid prototyping of industrial products or low cost and on-demand manufacturing from "open source designs" for both hobbyist and serious use. Both purposes include an idea of empowering individuals to create devices that are adapted to specific needs. Fab labs also can be part of Do-It-Yourself (DIY) communities, cultures and projects. (Kuznetsov, 2010)
The Fab@Home project emphasizes freedom of design and innovation of a Solid Freeform Fabrication system:
In a similar way IFTF, in the Future of Making Map argues:
Hands-on future is a word play that summarized the idea that is now spreading on the Internet and in venues such as the LIFT France '09 conference. According to Laurent Haug,
What happened in the software industry - young guys waking up with an idea, ending up changing the world from their sofa like it happened with Google, Amazon, Facebook, etc. - is now happening in the tangible world. Things like Arduino are enabling hackers and creators all around the globe, and what was possible with software (easily assemble code to create new applications) is now possible with objects. The conference program was centered around three main topics:
- Changing Things: Towards objects that are not just “smart” and connected, but also customizable, hackable, transformable, fully recyclable… Towards decentralized and multipurpose manufacturing, or even home fabrication…
- Changing Innovation: Towards continuous and networked innovation, emerging from users as well as entrepreneurs, from researchers as well as activists…
- Changing the Planet: Towards a “green design” that reconnects global environmental challenges with growth, but also with human desire, pleasure, beauty and fun ...
The Fab Lab concept emerged at MIT under the direction of N. Gershenfeld. It included a laser cutter, a miniature milling machine and jigsaw cutting machine. At the same time, people started thinking about creating cheap 3D printers.
The Fab Lab movement also is anchored in ecological thinking. “Think of RepRap as a China on your desktop” (Chris di Bona). Typical materials used in desktop fabrication are not much polluting and there is no transportation cost. The technology will also allow to produce cheap goods that are locally adapted. Finaly, designs can be shared for free, which means that "fab labs" rely on open content, both for the design of the tools and the designs that these tools then can "print".
A possible future was described by Vilbrandt et al (2008) as Universal Desktop Fabrication. “Advances in digital design and fabrication technologies are leading toward single fabrication systems capable of producing almost any complete functional object. We are proposing a new paradigm for manufacturing, which we call Universal Desktop Fabrication (UDF), and a framework for its development. UDF will be a coherent system of volumetric digital design software able to handle infinite complexity at any spatial resolution and compact, automated, multi-material digital fabrication hardware. This system aims to be inexpensive, simple, safe and intuitive to operate, open to user modification and experimentation, and capable of rapidly manufacturing almost any arbitrary, complete, high-quality, functional object. Through the broad accessibility and generality of digital technology, UDF will enable vastly more individuals to become innovators of technology, and will catalyze a shift from specialized mass production and global transportation of products to personal customization and point-of-use manufacturing. Likewise, the inherent accuracy and speed of digital computation will allow processes that significantly surpass the practical complexity of the current design and manufacturing systems. This transformation of manufacturing will allow for entirely new classes of human-made, peer-produced, micro-engineered objects, resulting in more dynamic and natural interactions with the world.” (Abstract, retrieved 17:30, 25 June 2009 (UTC)).
In October 2008, Evan Malone, the principal designer and implementor of Fab@Home, posted a (draft) Functional Block Diagram for FutureFab System at NextFab and that is shown below.
This diagram shows the complexity of software and hardware constraints interaction. Current fabbers can't produce "anything", but near future systems will be able to integrate both solid freeform fabrication (printing 3D objects) and electronic components
History
An excellent source for the early history of 3-D models is Lipson et al, 2004). According to this paper, “Physical models of machines have played an important role in the history of engineering for teaching, modeling, and exploring mechanical concepts. Many of these models have been replaced by computational representations, but new rapid-prototyping technology allows reintroduction of physical models as an intuitive way to demonstrate mechanical concepts” (Lipson et al, 2004:1032).
Here are a few milestones (that should be completed):
- 15th century
- Filippo Brunelleschi 1377–1436, the architect and engineer of the Duomo in Florence is known to have created construction models.
- 19th century
- Robert Willis (1800–1875) of Cambridge was known for his kinematic teaching models.
- Franz Reuleaux (1829–1905) created the world’s largest collection of kinematic models at the Technical University of Berlin with over 800 models.
- 1940's
- Birth of numerical control, i.e. machine tools controlled by code.
- mid 1950's
- Birth of special purpose programming languages for computer numerical controlled (CNC) machine tools.
- end 1950's - mid 1960's
- Birth of interfaces of Computer-aided design (CAD) with CNC.
- 1970
- Mohamed Hashish created a technique to add abrasives to the water jet cutter
- 1986
- Emergence of 3D-Printing
- 2005
- Neil Gershenfeld's et al. MIT class 863.04 - how to make (almost) anything.
- 2006
- The RepRap prototype
- 2007
- Neil Gershenfeld and Joe Jacobson MIT class How To Make Something That Makes (almost) Anything.
- 2008
- First partial DY 3D printer kits
- 2009
- First complete DYI 3D printer kits, e.g. the RapMan V3.1
- 2011
- A large number of full, small and mini fablabs in the World (about a 100 are listed in the fablab wiki
- 2012
- 3D printers become consumer appliances
Hardware tools
There exist several popular fab lab technologies, some of which are described below in more details. Most fall in the category of solid freeform fabrication tools and that include:
- 3D printers
- Laser cutters
- CNC machines
- Automated paper cutters
- 3D Scanners (for replication)
- Laser sintering
- embedded systems building blocks: Another kind of toolkits are electronics platforms like Arduino.
A fabber (or digital fabricator) refers to a "factory in box" (i.e. one of the above tools) that can create things automatically from digital data. The Digital Fabrication Portal distinguishes three fundamental kinds of fabbers, according to the way they operate on their raw material:
- Subtractive: Material is carved away from a solid block, such as by milling, turning, or electrodischarge machining (EDM). Subtractive fabbers have been automated since the late 1940s, and are often called computer-numerically controlled (CNC) machines.
- Additive: Material is successively added into place to build up the desired object. The methods used include selective curing, selective sintering, and aimed deposition. The first commercial additive fabber was introduced in 1987. * Formative: Material is neither added nor removed, but opposing pressures are applied to the material to modify its shape. Techniques in this category, including automated bending and reconfigurable molding, are under development.
- Hybrid: Processes from two or more of the above categories are combined. Sheet-based fabbers, which cut and laminate successive layers of sheet material, are hybrid subtractive/additive devices. A combination CNC punch press and press brake is a hybrid subtractive/formative fabber. (retrieved 17:25, 24 June 2009 (UTC)).
As of May 2009, there seemed to be three kinds of fab labs
- Fairly expensive setups (USD 60K range) that focus a lot on electronics and a large tool set for working with materials. A typical example would be MIT's "FabCentral" Lab described in the Fab Lab inventory. An other big fab lab, the Waag Society (NL) includes a laser cutter, a milling machine, a Modela milling and scanning machine. a vinyl cutter, an lock stich machine and an embroidery machine. One June 2009, Waag listed about 30 labs of this type world-wide.
- Small setups that only have 2-3 machines, e.g. a simple 3D desktop printer. Since we expect these 3D printers to become cheaper and cheaper, other devices such as laser cutters also may become more affordable and therefore popular. Hobby mills are already cheap.
- "Other", e.g. third-world, hobbyist and artist labs who assemble things from various parts, e.g. an open source washing machine from bicycle parts, bamboo, a solar panel and a motor.
As of April 2019, there is more diversity:
- The fabfoundation lists a The Hardware and Software configuation for over $110K. Add an extra 50% for Europe to that. A good and safe laser cutter along can cost over 50K.
- Higher education institutions offer a reduced version of this, some some, e.g. the fabricarium (Lille university) come close.
- Some fablabs work with cheap technology, that is refurbished/adapted by engineers, e.g. a laser cutter can be bought for a 1/4 of the price, iff someone is capable of changing/adapting the electronics and software.
- Smaller fablabs, institutionally supported or not often are small spaces that may include only 3D printers, vinyl cutters and small engraving machines.
- Some are specialized, e.g. extensions of existing science or woodcrafts workshop.
- Some are portable (e.g. a big suitcase) or Buses.
- Some are techshops, e.g. more expensive professional prototyping and custom fabrication environments, e.g. the the techshops of LeroyMerlin in France. The USA "techshops" went broke.
- ...
We found it quite interesting that when wrote the version of this piece in 2009, the MIT and the Waag fab lab did not include 3D-printers in the description of their setup. That probably meant that these two communities lived on two different "planets". However, as of 2011, the "official" list of fab lab engines include a 3D printer.
Solid Freeform Fabrication overview
“Freeform Fabrication is a collection of manufacturing technologies with which parts can be created without the need for part-specific tooling. A computerized model of the part is designed. It is sliced computationally, and layer information is sent to a fabricator that reproduces the layer in a real material” (Laboratory of Freeform Fabrication, UTexas, retrieved 17:25, 24 June 2009 (UTC)). CreatItReal shows an animation of this principle. Typical commercial free form fabricators range between 20'000 and 300'000 $US although low-end 3D printers start at $5000 (June 2009). Open source kits are much cheaper if self-assembled (see 3D printing)
Low End Solid Freeform Fabrication tools, also called rapid prototype machines are usually a kind of 3D printers. “3D printing is a unique form of fabrication that is related to traditional rapid prototyping technology. A three dimensional object is created by layering and connecting successive cross sections of material. 3D printers are generally faster, more affordable and easier to use than other additive fabrication technologies. While prototyping dominates current uses, 3D printers offers tremendous potential for retail consumer uses.” (Wikipedia, retrieved 17:25, 24 June 2009 (UTC)).
Currently, low-end commercial 3D prototypers are becoming affordable for individuals who want to "play" or schools. On oct 2011, the cheapest 3D printer we found was at $2700 from Up! Open source systems cost much less (not counting assembly time) and assembled versions cost about $4000.
According to Wikipedia (retrieved 17:25, 24 June 2009), “Prototypes made by low-end commercial machines cost around US$2 per cubic centimeter to fabricate. The RepRap Project is on track to produce a 3D prototyping machine and free and open source accompanying software that costs about US$400 to build and which can fabricate objects at a cost of about US$0.02 per cubic centimeter.”
There exist various kinds of 3D printers, e.g. Inkjet-like where layers of powder (e.g. plaster, corn starch or resins) are selectively bonded or photopolymer machines that fix liquids with an UV flood lamp.
- Some low-cost fabbers (e.g. RepRaps) include a kind of "gun" that heats up polymer plastic from a filament and then extrudes a fine stream to build things.
- Another low-cost faber (Fab@Home) uses syringes that you can fill in with Epoxy or some kinds of food. Materials are pushed down by a piston. The Epoxy comes with a resin and a hardener that have to be mixed before filling up the syringe. Malone and Lipson (2007) describe in good detail the architecture of the Fab@Home solid freeform printer.
A similar more complex procedure is called fused deposition modeling (FDM) (Montaro, 2002) and is described more precisely by Lipson et al. (2004:1030): “The process creates a sequence of thermoplastic layers from a filament wound coil that is heated and extruded through a nozzle. The trajectory of the nozzle is derived from the triangle mesh, so as to raster scan and fill solid volumes. In order to create functioning mechanisms, a second, soluble release material is placed in the gaps between the movable parts.”
Low cost 3D Printers
This article present 3D printing at its beginning in the early 2000's. Also see 3D printing for a more up-to-date article.

Very low-cost non-proprietary 3D printers are often referred to as Fabbers (although the term includes other technologies, including high-end ones). There exist several projects with a high profile in the "web 2.0 sphere". Most printers use a "hot gun" plastic extruder, but other techniques are emerging, e.g. sugar sintering in the CandyFab project.
The Fab@Home project (retrieved June 2009) “is a project dedicated to making and using fabbers - machines that can make almost anything, right on your desktop. [...] Fabbers (a.k.a. 3D printers or rapid prototyping machines) are a relatively new form of manufacturing that builds 3D objects by carefully depositing materials drop by drop, layer by layer. With the right set of materials and a geometric blueprint, you can fabricate complex objects that would normally take special resources, tools and skills if produced using conventional manufacturing techniques. A fabber can allow you to explore new designs, email physical objects to other fabber owners, and most importantly - set your ideas free. Just as MP3s, iPods and the Internet have freed musical talent, we hope that blueprints and fabbers will democratize innovation.”. Fab@Home was conceived by Hod Lipson of Cornell University and designed and implemented by Evan Malone. Current development includes more people.
RepRap is another well known project. “RepRap is short for Replicating Rapid-prototyper. It is the practical self-copying 3D printer shown on the right - a self-replicating machine. This 3D printer builds the parts up in layers of plastic. This technology already exists, but the cheapest commercial machine would cost you about €30,000. And it isn't even designed so that it can make itself. So what the RepRap team are doing is to develop and to give away the designs for a much cheaper machine with the novel capability of being able to self-copy (material costs are about €500). That way it's accessible to small communities in the developing world as well as individuals in the developed world. Following the principles of the Free Software Movement we are distributing the RepRap machine at no cost to everyone under the GNU General Public Licence. So, if you have a RepRap machine, you can use it to make another and give that one to a friend...” (What is RepRap?, retrieved 17:25, 24 June 2009 (UTC)).
This RepRap 3D printer builds the parts up in layers of plastic with the help of a custom-made Thermoplast Extruder. Version 2 “takes a 3mm diameter filament of a polymer (the single white rod coming into the picture from the top, not to be confused with the pair of white 12V supply wires), forces it down a heated barrel, and then extrudes it as a melt out of a fine nozzle. The resulting thin stream is laid down in layers to form the parts that RepRap makes. The extruder should work up to a temperature of 250o Celsius”. It works with ABS (Lego-like plastic) and polylactic acid. (Thermoplast Extruder Version 2.0, retrieved 17:30, 25 June 2009 (UTC)). In the UK, a RepRap assembly kit with everything included, is available as RapMan (2009/2010).
The next version of RepRap (RepRap Version 2.0 "Mendel") had ambitious plans: “will have multiple write heads for working with a wide range of materials in a single reprapped object, and will have the ability to embed three-dimensional electrical circuitry inside mechanical parts. Mendel is still very much in the early stages of development, but the build instructions are themselves under construction at that link.”
The CandyFab project is a 3D freeform fabrication project that works with sintering of sugar and other low-melting point materials. This project is different from Fab@Home and RepRap in two ways. The fabricator can print a much larger printable volume but with a lower resolution and you may eat the product. The creators argue that “Sugar is a particularly good medium because it's easy to obtain, low in cost, kid friendly, water soluble, non-hazardous, non-toxic, non-intimidating, rigid despite having a low melting point, and may be suitable for making objects for lost sugar (like lost wax) investment casting. We also think that it may also be possible to make interesting food with this technology.” (Sneak preview: The Evil Mad Scientist 3D Printer Project, retrieved 17:30, 25 June 2009 (UTC)).
One interesting application of the CandyFab would be to create 3D models of statistical data to be shown in presentations (e.g. a workshop or a thesis defense). After discussion, participants could eat the research results and further discuss data quality and distribution.
W.H. Oskay summarizes the procedure as follows: “When the first layer is started, there is a bed of granulated sugar. The heat gun locally melts the top surface of the bed in one point, melting the sugar at that point. The heat gun then moves to the next point, melting the sugar there. If this is done in a number of points in a row, it begins to fill in a line of melted sugar [...]. The sugar only stays molten for about 15-30 seconds after the heat gun is removed from a point. If a second line of melted sugar is added next to the first, you can begin to fill in an area with a thin layer of fused sugar. Let's suppose that you were making a cylinder-- then the first layer would just be a circle. The depth of the melt layer is controlled by the temperature, air flow rate, and hold time at each pixel location. After the first layer is finished, the bed is lowered slightly-- by an amount equal to the melt depth-- and a fresh layer of sugar is added to the top, such that the new top surface is at the same place where the original surface was. To make the next step in the cylinder, a new circle is drawn in the sugar on this layer. For each point in the circle, as the sugar in the top layer melts, it fuses to the corresponding point in the hardened sugar circle below. If we were to let the model cool and take it out of the machine at this point, you would have a solid thin disk, twice the thickness of the melt layer.”
Until recently, Solid Freeform fabbers had to be assembled by the end-user using open designs and low-level parts, i.e. many many days of bricolage. However, some fabbers now can be bought commercially as easy kits or fully assembled. E.g. in June 2009, the NextFab Store sold kits for about $3000 and assembled Fab@Homes for about $4000. Bits from Byte sold a (unassembled) RepRap kit (Version 3 - RapMan) for about £750. Read the RapMan entry for additional information. On June 2009, Cupcake from MakerBot Industries sold for £750 (unassembled). Malone and Lipson (2007) published an interesting breakdown of the cost of the model 1 fab@home 3D printer. Part costs were about $2300 USD plus about 18 hours of assembly work.
Within just three years, 3D printing became increasingly popular and as of 2011, several end-user machines are available. Prices started dropping a lot, i.e. commercial kits can be had for $1000 or less as you can see in the 3D printing article.
There also exists a low-cost Laminated Object Manufacturing engines that works with paper. Such a printer can use standard sheets of printer paper and will deposits in a pattern determined by the design. Another sheet of paper is added, and a blade then cuts away the excess paper. Such systems however, were too expensive (e.g. the Matrix 3D may sell for about $20'000).
Cutters
- Cutters / plotters
- Use a small blade to cut paper, cardstock, vinyl, fabrics etc. They can be bought for as little as $300. E.g. see the list in Bart Bakker's Vinyl cutter / plotter page. A popular entry-level model is the Silhouette Cameo.
- Laser cutters and engravers
- Laser cutters and engravers can process any non-metal material (e.g. acrylic, ceramics, cork, fiberglass, glass, plastic, leather, paper, stone, wood). “Laser cutting is a technology that uses a laser to cut materials, which is used in the production line and is typically used for industrial manufacturing applications. Laser cutting works by directing the output of a high power laser, by computer, at the material to be cut. The material then either melts, burns, vaporizes away, or is blown away by a jet of gas, [1] leaving an edge with a high quality surface finish. Industrial laser cutters are used to cut flat-sheet material as well as structural and piping materials.” (Wikipedia, retrieved 17:25, 24 June 2009 (UTC)).
According to Bart Bakker (oral communication, dec 2011), Laser cutters are the most popular tools in Netherland's fablabs. Laser cutters can't be used in closed rooms (i.e. needing air filtering). They also are expensive, although some exciting developments are out there, in particular LAOS, i.e. an open source replacement board and software that could be use to drive cheap chinese hardware.
- Laminated Object Manufacturing (LOM)
- “Laminated object manufacturing (LOM) is a rapid prototyping system developed by Helisys Inc. (Cubic Technologies is now the successor organization of Helisys) In it, layers of adhesive-coated paper, plastic, or metal laminates are successively glued together and cut to shape with a knife or a laser cutter.” (Wikipedia, retrieved 17:30, 25 June 2009 (UTC))
- Plasma cutters
- “Plasma cutting is a process that is used to cut steel and other metals of different thicknesses (or sometimes other materials) using a plasma torch. In this process, an inert gas (in some units, compressed air) is blown at high speed out of a nozzle; at the same time an electrical arc is formed through that gas from the nozzle to the surface being cut, turning some of that gas to plasma. The plasma is sufficiently hot to melt the metal being cut and moves sufficiently fast to blow molten metal away from the cut. Plasma can also be used for plasma arc welding and other applications.” (Wikipedia, retrieved 17:25, 24 June 2009 (UTC)).
Plasma cutters come in various sizes and are available from $3000.
- Water jet cutter
- “A water jet cutter is a tool capable of slicing into metal or other materials using a jet of water at high velocity and pressure, or a mixture of water and an abrasive substance. The process is essentially the same as water erosion found in nature but greatly accelerated and concentrated. It is often used during fabrication or manufacture of parts for machinery and other devices” (Wikipedia, retrieved 21:22, 23 June 2009 (UTC).)
According to Wikipedia, water jets can cut with a with of about 1mm and can cut materials such as rubber, foam, plastics, composites, stone, glass, tile, metals, food, paper and much more. Also, water jets can cut material without much harming or changing the materials' structures since there is no heat. I also can be considered a green technology, since it doesn't produce harmful waste. Water and abrasives can be recycled.
- Shopbots
- Computer-controlled ShopBots are do-all tool for precisely cutting, carving, drilling or machining all kinds of things from all kinds of materials. “A ShopBot is like a large plotter that moves pens around the surface (in X and Y axes) to create a drawing. Only a ShopBot moves a cutter around a big table (X and Y axes) and moves it up and down as well (Z axis) allowing it to make 3D movements and cut all sorts of shapes. The cutter looks like a drill bit and is spun by a motor called a router or spindle. Unlike a drill bit, a router bit is designed to cut from the sides as well as the tip. By precisely moving the cutter through material, a ShopBot CNC tool can create virtually any pattern or shape and will do it in materials such as wood, plastic, foam, aluminum and many composites.” (What's All the Excitement About ShopBot CNC Tools?, retrieved 17:30, 25 June 2009 (UTC)). Prices start at $7500.
- Combined mill / cutter / printer
Various technology can be combined into 3-axis CNC robots. As an example: “micRo is a unique system which can be used for both additive (printing) and subtractive (milling, cutting) fabrication. It is a precise, modular tool which allows you to create complex objects out of wood, metal, plastic and more”
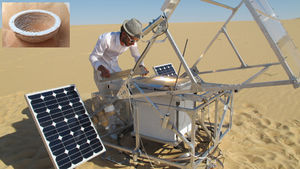
Selective Laser sintering
“In the Selective Laser Sintering (SLS) process, three-dimensional parts are created by fusing (or sintering) powdered thermoplastic materials with the heat from an infrared laser beam.” (Selective Laser Sintering (SLS), SLS Prototype, retrieved 17:25, 24 June 2009 (UTC)).
- “Selective laser sintering is an additive rapid manufacturing technique that uses a high power LASER (for example, a carbon dioxide laser) to fuse small particles of plastic, metal, ceramic, or glass powders into a mass representing a desired 3-dimensional object. The laser selectively fuses powdered material by scanning cross-sections generated from a 3-D digital description of the part” (Wikipedia, retrieved 17:25, 24 June 2009 (UTC)).
This technology if fairly complex and expensive compared to low-end 3D printers that extrude plastic. However, Markus Kayser in his SolarSinter demoed a cool bricolage version that sinters sand with solar energy. Also, commercial laser sintering printers should probably soon be available for less than 10K. (dec/2011).
Stereolithography (SLA)
Stereolithography (or photopolymerization) “is a common rapid manufacturing and rapid prototyping technology for producing parts with high accuracy and good surface finish. A device that performs stereolithography is called an SLA or Stereolithography Apparatus.” (Wikipedia, retrieved 17:25, 24 June 2009 (UTC)).
SLA is too expensive for fab labs (between $100,000 and $400,000)
CNC mills
A milling machine (fr. "fraiseuse") is a machine tool used for the shaping of metal and other solid materials. It uses rotating cutters to cut stuff from a workpiece. In more sophisticated milling machines, both the cutters and the workpiece can be rotated in three axis.
CNC Hobby Mills
See also:
- hobby milling
- Shopbots above
A whole variety of hobby mills are now available and work with softer materials, e.g. the Roland iModela iM-01 Hobby Mill. According to the product announcement page, retrieved 14:33, 7 December 2011 (CET), the iModela is an inexpensive (about $1000), easy-to-use desktop device that mills wax, foam, balsa wood and plastic materials commonly used in craft and hobby projects. The iCreate web site includes a few sample designs plus other support materials. This model can read IGES, DXF and STL and only works with Windows.
Computer controlled embroidery machines
A computer-controlled embroidery machine allows to print out complex designs, e.g. embroidery.
3D Scanners
An alternative to designing objects is to scan them. Rotating 3D scanners can be bought for about $3000, but hand-held Laser 3D scanning costs next to nothing (see the links section below for pointers).
Electronic kits
See also: Embedded systems building blocks, often that kind of hardware is specially made for education.
- Arduino
Arduino “is an open-source electronics prototyping platform based on flexible, easy-to-use hardware and software. It's intended for artists, designers, hobbyists, and anyone interested in creating interactive objects or environments.
Arduino can sense the environment by receiving input from a variety of sensors and can affect its surroundings by controlling lights, motors, and other actuators. The microcontroller on the board is programmed using the Arduino programming language (based on Wiring) and the Arduino development environment (based on Processing). Arduino projects can be stand-alone or they can communicate with software on running on a computer (e.g. Flash, Processing, MaxMSP).” (Arduino Home Page, retrieved 17:25, 24 June 2009 (UTC)).
- OpenMoko
OpenMoko is is a project dedicated to delivering mobile phones with an open source software stack. Openmoko is currently (June 2009) selling the Neo FreeRunner phone to advanced users and will start selling it to the general public as soon as the software is more developed.
“The Openmoko stack, which includes a full X server, allows users and developers to transform mobile hardware platforms into unique products. Our license gives developers and users freedom to cosmetically customize their device or radically remix it; change the wallpaper or rebuild the entire house! It grants them the freedom, for example, to transform a phone into a medical device or point of sale device or the freedom to simply install their own favorite software. Beyond freeing the software on our devices we have also released our CAD files. And at LinuxWorld 2008, we announced the release of the schematics for our products.” (Introduction, retrieved 17:30, 25 June 2009 (UTC)).
- The Make controller kit
The Make Controller Kit sponsored by Make magazine, is an open source hardware solution for hobbyists and professionals to create interactive applications. It supports desktop interfaces via a variety of languages such as Max/MSP, Flash, Processing, Java, Python, Ruby, or anything that supports Open Sound Control (OSC).
Software
See
Links
Fab Lab portals and overviews
- FabCentral, The Center for Bits and Atoms, MIT. Inventor of FabLab classes.
- Fab Lab FAQ, MIT. (includes further pointers).
- How to make (almost) anything (alex schaub's mas863 log Fall 2008). Illustrates what could be done.
- The FabLab@School, created by Prof. Paulo Blikstein at Stanford University is a new type of digital fabrication lab especially designed for schools and children, with several special characteristics.
- High-Low Tech group (MIT Media Lab). Explore the intersection of computation, physical materials, manufacturing processes, traditional crafts, and design.
- Wikipedia articles
- Wikipedia
- Category:Solid freeform fabrication (Wikipedia).
- Desktop manufacturing (Wikipedia)
- Digital fabricator (Wikipedia)
- Fabber (Wikipedia).
- Solid freeform fabrication (Wikipedia, overview).
- Overviews
- On the future of invention, by Neil Gershenfeld, Seedmagazine, June 24, 2009.
- Desktop manufacturing - Helping poor-world inventors, The Economist, Mar 23 2005.
- What is a Fabber?, An Introduction to the 21st Century, Ennex Corporation, retrieved 17:25, 24 June 2009 (UTC).
- The Hacker Ethic and the Spirit of the Information Age by Pekka Himanen (book excerpt)
- Mitch Altman on "The Hackerspace Movement" (TEDx talk video, Brussels, 2012).
Repositories
- Models (designs in some format that can be "printed")
- New objects (includes visualization and downloadable files)
- 3dprintables.org (excellent wiki includes educational objects, often with links models on external sites)
- thingiverse (a place to share digital designs that can be made into real, physical objects). Many interesting objects for RepRap machines like the RapMan
- Open Prosthetics Project is producing useful innovations in the field of prosthetics and freely sharing the designs
- Opendesk (Furniture)
- How-to
- Instructables Instructions on how to build various things
- Hardware models
- KMODDL. Some open source models are available in the Machines and Mechanisms Wiki
3D printing
See 3D printing
Numerical control
- Numerical control (Wikipedia)
Cheap 3D scanning
- David Laserscanner, A complete system with calibration panels, camera, red laser and software is about 350 Euros. But you also can buy just parts, e.g. the 90.- red laser and build the rest yourself. The software includes scanning, interpolation, some editing and shape fusion with various methods. To the right you can see a picture of one scan, i.e. our first attempt using this system - Daniel K. Schneider 17:36, 8 December 2009 (UTC)
Other Fab Lab hardware
Laser and plasma cutters
- How Plasma Cutters Work (Howstuffworks.com).
Water jets
CNC mills
- The CNC mill project
- Lumenlab's lowcost 3D CNC milling/cutting/printing systems
- Guerrilla guide to CNC machining and resin casting Good, detailed tutorial.
CNC shopbots
- Shopbottools.com. E.g. have a look at the portfolio of projects (including school contexts). Prices are from $7500 to $20K.
Selective Laster Sintering (SLS)
Stereolithography (SLA)
- Stereolithography (SLA), Castle Island Co., retrieved 17:25, 24 June 2009 (UTC)
Electronics
In order to avoid hassles with repairs and an such, it is probably a good idea to buy in your own country. E.g. in Switzerland, there is the dshop (an Arduino/OpenMoko vendor)
- Arduino
- Arduino (Home page)
- YouTube Videos
- Most Arduino products are I/O Boards on top of which one can insert shields (extensions). Various parts range from cheap to $400.-. See the vendor page. Some OpenSource 3D fabbers use these boards.
- There exist many Arduino clones (since the design is open source). See the Wikipedia page.
- Arduino (Wikipedia).
- The Making of Arduino IEEE Spectrum, By David Kushner / October 2011
- OpenMoko
- Openmoko is a project dedicated to delivering mobile phones with an open source software stack. It can run with various OSs, e.g. it got official Debian support and also runs with Android.
- OpenMoko (Home page)
- TechTree review of Freerunner
- OpenMoko Store. The FreeRunner (A6) model is sold for $250.
- Make Controller Kit
Make Controller Kit online sales at Making Things.com
New technology mags, blogs and communities
(Closely or loosely related to fablabs)
- Make the future (Waag society/ United Nations Development Programme, UNDP)
- SEED magazine
- NewScientist (tech section)
- FabLabs - a space for those tinkering with Fab Labs
- Thingiverse. Is a place for you to share your digital designs with the world.
- Hacked Gadgets
- NYC Resistor is a hacker collective with a shared space located in downtown Brooklyn.
- Next Big Future (blog)
- Pasta&Vinegar, Nicolas Nova, LiftLab (mind/tech bazar from outer space blog).
- The LIFT conference series (organized by our friends from LiftLab).
- Make magazine (The most popular commercial geeky do it yourself magazine)
- MakingThings (project page)
- Low Tech Magazine. for ideas
- Fab ✱ Manchester 2012 (conference)
- FabLearn 2012
- OpenSourceEcology.org, high-performance, modular, do-it-yourself, low-cost platform - that allows for the easy fabrication of the 50 different industrial machines that it takes - to build a small, sustainable civilization with modern comforts.
Fab Labs
- Fab Lab Central (MIT, USA). Includes pointers to many FabLabs world-wide.
- Fablab Amsterdam (Netherlands)
- Laboratory for Freeform Fabrication (UTexas, USA).
- FabLab Squared (France)
- miniFABLAB (Netherlands)
- Creating Living Lab (Hochschule Luzern, Switzerland) and Fablab (Luzern)
Mobile fablabs
There exist a number of solutions, i.e. several organizations do have buses that include fablab.
- Fablab en kit offers a big foldable container that can fit into a mini-van.
Bibliography
See also digital design and fabrication bibliography and fab labs in education
- Bereza, Marek (2007). Rise of the Replicator: The Evolution of Media Into The Tangible. The Royal College of Art, Master thesis. PDF
- Blikstein, Paolo, Sylvia Libow Martinez, and Heather Allen Pang (eds). (2016). Meaningful Making: Projects and Inspirations for Fab Labs + Makerspaces, CONSTRUCTING MODERN KNOWLEDGE PRESS, Print book ISBN: 978-0- 9891511-9-1, e-book ISBN: 978-0- 9891511-2- 2, http://fablearn.stanford.edu/fellows/page/meaningful-making-book.
- Breen, Jack; Robert Nottrot, Martijn Stellingwerff (2003). Tangible virtuality--perceptions of computer-aided and physical modelling, Automation in Construction, Volume 12, Issue 6, Design e-ducation: Connecting the Real and the Virtual, November 2003, Pages 649-653, ISSN 0926-5805, DOI: 10.1016/S0926-5805(03)00053-0.
- Burns M., (1995) The Freedom to Create, in Technology Management, Volume 1, Number 4 http://www.ennex.com/~fabbers/publish/199407-MB-FreedomCreate.asp
- Bowyer, Adrian (2007) Why Accountants are Dull and Guitarists are Glamourous - The End of Intellectual Property, Time Compression Technology Magazine, volume 15, issue 3, p33 (2007).
- Bowyer, Adrian (2007)- The Self-replicating Rapid Prototyper ─ Manufacturing for the Masses, Invited Keynote Address, Proc. 8th National Conference on Rapid Design, Prototyping & Manufacturing, Centre for Rapid Design and Manufacture, High Wycombe, June 2007. Rapid Prototyping and Manufacturing Association, ISBN-13: 978-0948314537 (2007).
- Bowyer, Adrian (2007). Breed your own Design, Icon Magazine, volume 52, October 2007.
- Burry, Mark; Michael Ostwald, Peter Downton, Andrea Mina, (2007) Homo Faber - Modelling Architecture, Sydeney: Archadia Press, ISBN 9780977571123. PDF (See also the video: Thinking modeling making
- Ceccarelli, M., (Ed.) 2000, International Symposium on History of Machines and Mechanisms, Proc. HMM Kluwer Academic, Dordrecht.
- Cohen D. L., Malone E., Lipson H., Bonassar L., (2006) "3D direct printing of heterogeneous tissue implants", Tissue Engineering, Vol. 12, No. 5: 1325-1335
- Editors' Review (2005). Desktop Factories - FAB The Coming Revolution on Your Desktop -- from Personal Computers to Personal Fabrication By Neil Gershenfeld, Basic Books, Business Week, May 2 2005.
- Evil Mad Scientist Laboratories (2007). Solid freeform fabrication: DIY, on the cheap, and made of pure sugar, http://www.evilmadscientist.com/article.php/candyfab, retrieved 17:30, 25 June 2009 (UTC).
- Flichy, Patrice (2010), Le sacre de l'amateur : Sociologie des passions ordinaires à l'ère numérique, Seuil.
- Gershenfeld N. Think Globally, fabricate locally, PrincipalVoices.com. PDF (reprint)
- Gershenfeld, Neil, A., (2005) FAB: The Coming Revolution on Your Desktop – From Personal Computers to Personal Fabrication, Basic Books, ISBN 0-465-02745-8.
- Institute of the Future (2009). The future of making, PDF
- Kuznetsov, Stacey and Eric Paulos (2010). Rise of the Expert Amateur: DIY Projects, Communities, and Cultures, Proceedings of ACM NordiCHI 2010: Extending boundaris, Reykjavik, PDF preprint
- Jenweill, Mark, Fab Labs unshackle imaginations, USA Today, 11/6/2005.
- Moon, F. C., 2003a, Franz Reuleaux: Contributions to 19th Century Kinematics and Theory of Machines, Applied Mechanics Reviews, American Society of Mechanical Engineers, N.Y.
- Lillard, A. and Else-Quest, N. (2006) The Early Years: Evaluating Montessori Education Science, Vol. 313. no. 5795, pp. 1893 - 1894
- Lipson H., Moon F.C., Hai J., Paventi C., (2004) 3D-Printing the History of Mechanisms, ASME Journal of Mechanical Design, pp. 1029-1033. PDF
- Lipson H. (2005a) "Homemade: The future of Functional Rapid Prototyping", IEEE Spectrum, feature article, May 2005, pp. 24-31 http://www.mae.cornell.edu/ccsl/papers/Spectrum05_Lipson.pdf
- Lipson H. (2005b). "Homemade: The future of Functional Rapid Prototyping", IEEE Spectrum, feature article, May 2005, pp. 24-31.
- Lobovsky M., Lobovsky A., Behi M., Lipson H. (2008), "Solid Freeform Fabrication of Stainless Steel Using Fab@Home", Proceedings of the 19th Annual Solid Freeform Fabrication Symposium, Austin TX, Aug 2008. PDF
- Malone, E. (2006). Faxing Artifacts: The promise of three-dimensional scanning and rapid prototyping of archaeological materials, International Council of Archaeo-Zoologists – ICAZ 2006, Mexico City, Mexico, 23-28 Aug 2006, Poster.
- Malone E., Lipson H., (2006) "Freeform Fabrication of Ionomeric Polymer-Metal Composite Actuators", Rapid Prototyping Journal, Vol. 12, No. 5, pp.244-253.
- Malone E., Lipson H., (2007) "Fab@Home: The Personal Desktop Fabricator Kit", Rapid Prototyping Journal, Vol. 13, No. 4, pp.245-255. PDF. (This is to our knowledge the best easy to read article explaining most aspects of a desktop fabricator).
- Malone E., Rasa K., Cohen D. L., Isaacson T., Lashley H., Lipson H., (2004) "Freeform fabrication of 3D zinc-air batteries and functional electro-mechanical assemblies", Rapid Prototyping Journal, Vol. 10, No. 1, pp. 58-69.
- Malone, E., Berry, M., Lipson, H., (2008), "Freeform Fabrication and Characterization of Zinc-air Batteries", Rapid Prototyping Journal, Vol. 14, No. 3, pp. 128-140. PDF
- Apoorva Mandavilli (2006). Appropriate technology: Make anything, anywhere, Nature 442, 862-864 (24 August 2006). doi:10.1038/442862a.
- McMains, S. (2005). "Layered Manufacturing Technologies", Comm. ACM, Volume 48, Number 6, pp 50-56.
- Mikhak, Bakhtiar; Christopher Lyon, Tim Gorton, Neil Gershenfeld, Caroline McEnnis and Jason Taylor (unknown). Fab Lab: An Alternate Model Of Ict For Development, PDF
- Milanese, Fiona (2006). FABLab allows you to create the gadget of your dreams, Science in Africa. August 2006, HTML
- Montaro, M. et al., 2002, “Material Characterization of Fused Deposition Modeling (FDM) ABS by Designed Experiments,” University of California, Berkeley Report.
- Sells, Ed; Zach Smith, Sebastien Bailard, and Adrian Bowyer (2007). RepRap: The Replicating Rapid Prototyper - Maximizing Customizability by Breeding the Means of Production. Extended abstract in Proc. Mass Customization and Personalization Conference, MIT, October 2007.
- STEEG, T., 2008. Makers, Hackers and Fabbers: what is the future for D&T? IN: Norman, E.W.L. and Spendlove, D. (eds.). The Design and Technology Association International Research Conference, [Loughborough University, 2-4 July]. Wellesbourne : The Design and Technology Association, pp. 65-73. 08.pdf PDF - HTML Abstract. (includes throughts about Design and Technology teaching)
- Thomson, Clive (2008). Build It. Share It. Profit. Can Open Source Hardware Work? Wired Magazine, 16:1
- Touchgraphics, Inc. (2009). An Interactive Talking Campus Model at Carroll Center for the Blind, Final Report, center talking campus model final report low.pdf PDF. (Objects were created with a commercial 3D printer).
- Vilbrandt, T., Malone, E., Lipson H., Pasko, A., (2008) "Universal Desktop Fabrication", in Heterogeneous Objects Modeling and Applications, pp. 259-284. DOI: 10.1007/978-3-540-68443-5 (Access restricted)
- Links
- Adrian Bowyer's Publications
- Evan Malone's publications
- Cornell Computational Synthesis Laboratory publications
- Craft Technology publications (University of Colorado, Boulder)
Acknowledgment
Thanx to Nicolas Nova for inviting Daniel K. Schneider to LIFT France '09 which gave me the impulse for writing a first version of this piece and to explore various sub topics in more depth.