Fab lab: Difference between revisions
m (using an external editor) |
m (using an external editor) |
||
Line 7: | Line 7: | ||
Fab labs are a [[disruptive technology]]. | Fab labs are a [[disruptive technology]]. | ||
See also: [[Constructionist learning object]]s and [[Fröbel gifts]], i.e. educational application areas with huge potential for desktop fabbers. '''Disclaimer''': I am not a "fab lab" expert and some technical information may be wrong. However, there should be enough good links that you could follow up - [[User:Daniel K. Schneider|Daniel K. Schneider]] 13: | See also: [[Constructionist learning object]]s and [[Fröbel gifts]], i.e. educational application areas with huge potential for desktop fabbers. '''Disclaimer''': I am not a "fab lab" expert and some technical information may be wrong. However, there should be enough good links that you could follow up - [[User:Daniel K. Schneider|Daniel K. Schneider]] 13:43, 25 June 2009 (UTC). | ||
Fab labs can have different aims, e.g. rapid prototyping or low cost and on-demand manufacturing from "open source designs" for both hobbyist and serious use. Both purposes include an idea of empowering individuals to create devices that are adapted to specific needs. | Fab labs can have different aims, e.g. rapid prototyping or low cost and on-demand manufacturing from "open source designs" for both hobbyist and serious use. Both purposes include an idea of empowering individuals to create devices that are adapted to specific needs. | ||
Line 26: | Line 26: | ||
The Fab Lab movement also is anchored in ecological thinking. {{quotation|Think of RepRap as a China on your desktop}} (Chris di Bona). Materials used are no much polluting and there is no transportation cost. | The Fab Lab movement also is anchored in ecological thinking. {{quotation|Think of RepRap as a China on your desktop}} (Chris di Bona). Materials used are no much polluting and there is no transportation cost. | ||
A possible future was described by Vilbrandt et al (2008) {{quotation|Advances in digital design and fabrication technologies are leading toward single fabrication systems capable of producing almost any complete functional object. We are proposing a new paradigm for manufacturing, which we call Universal Desktop Fabrication (UDF), and a framework for its development. UDF will be a coherent system of volumetric digital design software able to handle infinite complexity at any spatial resolution and compact, automated, multi-material digital fabrication hardware. This system aims to be inexpensive, simple, safe and intuitive to operate, open to user modification and experimentation, and capable of rapidly manufacturing almost any arbitrary, complete, high-quality, functional object. Through the broad accessibility and generality of digital technology, UDF will enable vastly more individuals to become innovators of technology, and will catalyze a shift from specialized mass production and global transportation of products to personal customization and point-of-use manufacturing. Likewise, the inherent accuracy and speed of digital computation will allow processes that significantly surpass the practical complexity of the current design and manufacturing systems. This transformation of manufacturing will allow for entirely new classes of human-made, peer-produced, micro-engineered objects, resulting in more dynamic and natural interactions with the world.}} ([http://www.springerlink.com/content/23k0072182021620/?p=e1bfbcc3e9ab4153ab364d31bf57330c&pi=10 Abstract], retrieved 13: | A possible future was described by Vilbrandt et al (2008) {{quotation|Advances in digital design and fabrication technologies are leading toward single fabrication systems capable of producing almost any complete functional object. We are proposing a new paradigm for manufacturing, which we call Universal Desktop Fabrication (UDF), and a framework for its development. UDF will be a coherent system of volumetric digital design software able to handle infinite complexity at any spatial resolution and compact, automated, multi-material digital fabrication hardware. This system aims to be inexpensive, simple, safe and intuitive to operate, open to user modification and experimentation, and capable of rapidly manufacturing almost any arbitrary, complete, high-quality, functional object. Through the broad accessibility and generality of digital technology, UDF will enable vastly more individuals to become innovators of technology, and will catalyze a shift from specialized mass production and global transportation of products to personal customization and point-of-use manufacturing. Likewise, the inherent accuracy and speed of digital computation will allow processes that significantly surpass the practical complexity of the current design and manufacturing systems. This transformation of manufacturing will allow for entirely new classes of human-made, peer-produced, micro-engineered objects, resulting in more dynamic and natural interactions with the world.}} ([http://www.springerlink.com/content/23k0072182021620/?p=e1bfbcc3e9ab4153ab364d31bf57330c&pi=10 Abstract], retrieved 13:43, 25 June 2009 (UTC)). | ||
In october 2008, Evan Malone, the principal designer and implementor of Fab@Home, posted a (draft) [Functional Block Diagram for FutureFab System] at NextFab and that is shown below. | In october 2008, Evan Malone, the principal designer and implementor of Fab@Home, posted a (draft) [http://nextfab.org/files/draft-functional-block-diagram-futurefab-system Functional Block Diagram for FutureFab System] at NextFab and that is shown below. | ||
[[image:SFF_System_Process_Block_Diagram 2_1.jpg|thumb|800px|none|Functional Block Diagram for FutureFab System by Evan Malone (2008)]] | [[image:SFF_System_Process_Block_Diagram 2_1.jpg|thumb|800px|none|Functional Block Diagram for FutureFab System by Evan Malone (2008)]] | ||
Line 66: | Line 66: | ||
; 2007 | ; 2007 | ||
: Neil Gershenfeld and Joe Jacobson MIT class [http://fab.cba.mit.edu/classes/MIT/960.07/ How To Make Something That Makes (almost) Anything]. | : Neil Gershenfeld and Joe Jacobson MIT class [http://fab.cba.mit.edu/classes/MIT/960.07/ How To Make Something That Makes (almost) Anything]. | ||
: The CandyFab Project | |||
== Hardware tools == | == Hardware tools == | ||
Line 89: | Line 90: | ||
[[image:fab-at-home-fabber.jpg|thumb|400px|right|Fab@Home Fabber model 1, 2007: Source [http://www.fabathome.org/wiki/index.php?title=Image:IMG_0110.jpg fabathome.org]]] | [[image:fab-at-home-fabber.jpg|thumb|400px|right|Fab@Home Fabber model 1, 2007: Source [http://www.fabathome.org/wiki/index.php?title=Image:IMG_0110.jpg fabathome.org]]] | ||
{{quotation|Freeform Fabrication is a collection of manufacturing technologies with which parts can be created without the need for part-specific tooling. A computerized model of the part is designed. It is sliced computationally, and layer information is sent to a fabricator that reproduces the layer in a real material}} ([http://utwired.engr.utexas.edu/lff/ Laboratory of Freeform Fabrication], UTexas, retrieved 17:25, 24 June 2009 (UTC)). | {{quotation|Freeform Fabrication is a collection of manufacturing technologies with which parts can be created without the need for part-specific tooling. A computerized model of the part is designed. It is sliced computationally, and layer information is sent to a fabricator that reproduces the layer in a real material}} ([http://utwired.engr.utexas.edu/lff/ Laboratory of Freeform Fabrication], UTexas, retrieved 17:25, 24 June 2009 (UTC)). CreatItReal shows an [http://createitreal.com/pages/tech.html animation] of this principle. Typical commercial free form fabricators range between 20'000 and 300'000 $US although low-end 3D printers start at $5000 (June 2009). Open source kits are much cheaper if self-assembled (see below) | ||
Currently, low-end commercial 3D prototypers are still costly for individuals who want to "play" or schools. On June 2009, the cheapest 3D printer we found | Currently, low-end commercial 3D prototypers are still costly for individuals who want to "play" or schools. On June 2009, the cheapest 3D printer we found a printer at $5000 from Desktop Factory and one at 5000 Euros from CreateItReal. A more expensive one is "Dimension uPrint" and cost £12000. In addition you need to buy materials and solidifiers which may be more expensive. | ||
According to [http://en.wikipedia.org/wiki/RepRap_Project Wikipedia] (retrieved 17:25, 24 June 2009), {{quotation|Prototypes made by these low-end commercial machines cost around US$2 per cubic centimeter to fabricate. The RepRap Project is on track to produce a 3D prototyping machine and free and open source accompanying software that costs about US$400 to build and which can fabricate objects at a cost of about US$0.02 per cubic centimeter.}} | According to [http://en.wikipedia.org/wiki/RepRap_Project Wikipedia] (retrieved 17:25, 24 June 2009), {{quotation|Prototypes made by these low-end commercial machines cost around US$2 per cubic centimeter to fabricate. The RepRap Project is on track to produce a 3D prototyping machine and free and open source accompanying software that costs about US$400 to build and which can fabricate objects at a cost of about US$0.02 per cubic centimeter.}} | ||
Line 106: | Line 107: | ||
[[image:reprap.jpg|thumb|400px|right|RepRap self-replicating 3D printer]] | [[image:reprap.jpg|thumb|400px|right|RepRap self-replicating 3D printer]] | ||
[http://reprap.org/ RepRap] is another well know project. {{quotation|RepRap is short for Replicating Rapid-prototyper. It is the practical self-copying 3D printer shown on the right - a self-replicating machine. This 3D printer builds the parts up in layers of plastic. This technology already exists, but the cheapest commercial machine would cost you about €30,000. And it isn't even designed so that it can make itself. So what the RepRap team are doing is to develop and to give away the designs for a much cheaper machine with the novel capability of being able to self-copy (material costs are about €500). That way it's accessible to small communities in the developing world as well as individuals in the developed world. Following the principles of the Free Software Movement we are distributing the RepRap machine at no cost to everyone under the GNU General Public Licence. So, if you have a RepRap machine, you can use it to make another and give that one to a friend...}} ([http://reprap.org/bin/view/Main/WebHome What is RepRap?], retrieved 17:25, 24 June 2009 (UTC)). | [http://reprap.org/ RepRap] is another well know project. {{quotation|RepRap is short for Replicating Rapid-prototyper. It is the practical self-copying 3D printer shown on the right - a self-replicating machine. This 3D printer builds the parts up in layers of plastic. This technology already exists, but the cheapest commercial machine would cost you about €30,000. And it isn't even designed so that it can make itself. So what the RepRap team are doing is to develop and to give away the designs for a much cheaper machine with the novel capability of being able to self-copy (material costs are about €500). That way it's accessible to small communities in the developing world as well as individuals in the developed world. Following the principles of the Free Software Movement we are distributing the RepRap machine at no cost to everyone under the GNU General Public Licence. So, if you have a RepRap machine, you can use it to make another and give that one to a friend...}} ([http://reprap.org/bin/view/Main/WebHome What is RepRap?], retrieved 17:25, 24 June 2009 (UTC)). | ||
[[image:candyfab-sugarobjects.jpg|thumb|400px|right|CandyFab pur sugar objects]] | |||
The [http://www.candyfab.org/ CandyFab] project is a 3D freeform fabrication project that works with sugar and other low-melting point materials. This project is different from Fab@Home and RepRap in two ways. The fabricator can print a much larger printable volume but with a lower resolution and you may eat the product. The creators argue that {{quotation|Sugar is a particularly good medium because it's easy to obtain, low in cost, kid friendly, water soluble, non-hazardous, non-toxic, non-intimidating, rigid despite having a low melting point, and may be suitable for making objects for lost sugar (like lost wax) investment casting. We also think that it may also be possible to make interesting food with this technology.}} ([http://www.evilmadscientist.com/article.php/3printerpreview Sneak preview: The Evil Mad Scientist 3D Printer Project], retrieved 13:43, 25 June 2009 (UTC)). | |||
Until recently, fabbers had to be assembled by the end-user using open designs and low-level parts, i.e. many many days of bricolage. However, some fabbers now can be bought commercially as easy kits or fully assembled. E.g. in ''June 2009'', the [http://store02.prostores.com/servlet/kobask8/StoreFront NextFab Store] sold kits for about $3000 and assembled Fab@Homes for about $4000. [http://www.bitsfrombytes.com/ Bits from Byte] sold a (unassembled) [http://www.bitsfrombytes.com/index.php?option=com_content&view=article&id=77&Itemid=100006 ReRap kit] (Version 3 - RapMan) for about £750. | Until recently, fabbers had to be assembled by the end-user using open designs and low-level parts, i.e. many many days of bricolage. However, some fabbers now can be bought commercially as easy kits or fully assembled. E.g. in ''June 2009'', the [http://store02.prostores.com/servlet/kobask8/StoreFront NextFab Store] sold kits for about $3000 and assembled Fab@Homes for about $4000. [http://www.bitsfrombytes.com/ Bits from Byte] sold a (unassembled) [http://www.bitsfrombytes.com/index.php?option=com_content&view=article&id=77&Itemid=100006 ReRap kit] (Version 3 - RapMan) for about £750. | ||
Line 178: | Line 182: | ||
* [http://www.3dprintables.org/printables/index.php?title=STLGenerator STL Generator] | * [http://www.3dprintables.org/printables/index.php?title=STLGenerator STL Generator] | ||
* CandyFab developed [http://wiki.candyfab.org/CandyFab_Software CandyFaboulous], written in [http://processing.org/ Processing], an open source programming language and environment for people who want to program images, animation, and interaction. | |||
== Fab Labs and fabbers in education == | == Fab Labs and fabbers in education == | ||
Line 186: | Line 192: | ||
more contemporary concepts from aerodynamics to molecular biology.}} | more contemporary concepts from aerodynamics to molecular biology.}} | ||
Fab labs were born in higher education (e.g. Gershenfeld:2005) and most of these are sponsored by academic institutions. Of course, technical hobbyists always did exist and and in many countries, schools do offer facilities and even classes for all sorts of bricolage. The most prominent fabber projects were founded by academics. E.g. Reprap by [http://people.bath.ac.uk/ensab/ Adrien Bowyer] et al. at University of Bath (UK); Fab@Home by [http://nextfab.org/content/evan-malone Evan Malone] while he was a PhD student at Cornell. Commercial low-cost printers are sold as tool for design classes. E.g. a [http://www.desktopfactory.com/ Desktop Factory] printer is advertised as {{quotation|With the Desktop Factory 3D printer, departments within large firms will be able to have their own dedicated 3D printers, and many small businesses, design firms and schools will be able to own this capability for the first time. Professional designers, engineers and students alike will be able to build inexpensive models from their designs before committing to expensive, custom prototyping}} (retrieved 13: | Fab labs were born in higher education (e.g. Gershenfeld:2005) and most of these are sponsored by academic institutions. Of course, technical hobbyists always did exist and and in many countries, schools do offer facilities and even classes for all sorts of bricolage. The most prominent fabber projects were founded by academics. E.g. Reprap by [http://people.bath.ac.uk/ensab/ Adrien Bowyer] et al. at University of Bath (UK); Fab@Home by [http://nextfab.org/content/evan-malone Evan Malone] while he was a PhD student at Cornell. Commercial low-cost printers are sold as tool for design classes. E.g. a [http://www.desktopfactory.com/ Desktop Factory] printer is advertised as {{quotation|With the Desktop Factory 3D printer, departments within large firms will be able to have their own dedicated 3D printers, and many small businesses, design firms and schools will be able to own this capability for the first time. Professional designers, engineers and students alike will be able to build inexpensive models from their designs before committing to expensive, custom prototyping}} (retrieved 13:43, 25 June 2009 (UTC)). | ||
Knapp et al. (2007) stress the benefits of physical models in a variety of educational settings, e.g. Mathematics, anatonomy, molecular biology, aeronautics, chemistry, arehceology: {{quotation|Physical models have been shown to enhance learning in general student populations as well. Students learn in a variety of ways, and models allow students to include their sense of touch in the learning experience. The role of experience is emphasized in Piaget's description of cognitive development, that is, to know an object a subject must act on it and thus transform it - displace, connect, combine, take apart, and reassemble it. (Cohen, 1983). Science education especially benefits from the use of models. | Knapp et al. (2007) stress the benefits of physical models in a variety of educational settings, e.g. Mathematics, anatonomy, molecular biology, aeronautics, chemistry, arehceology: {{quotation|Physical models have been shown to enhance learning in general student populations as well. Students learn in a variety of ways, and models allow students to include their sense of touch in the learning experience. The role of experience is emphasized in Piaget's description of cognitive development, that is, to know an object a subject must act on it and thus transform it - displace, connect, combine, take apart, and reassemble it. (Cohen, 1983). Science education especially benefits from the use of models. | ||
Line 256: | Line 262: | ||
[[image:maker-campfire.jpg|thumb|200px|3D printer as geek campfire (Source:[http://blog.makerbot.com/2009/04/27/maker-revolution-gathering-round-the-makerbot-campfire/])]] | [[image:maker-campfire.jpg|thumb|200px|3D printer as geek campfire (Source:[http://blog.makerbot.com/2009/04/27/maker-revolution-gathering-round-the-makerbot-campfire/])]] | ||
{{quotation|We didn’t know it, but it turns out that sitting around a table with folks while the MakerBot Cupcake CNC is puttering away and doing its thing and making objects appear where there were none before is really a great community activity! One of the gatherers mentioned that it felt like a geek campfire and it did!}} ([http://blog.makerbot.com/2009/04/27/maker-revolution-gathering-round-the-makerbot-campfire/ Pre Pettis], retrieved 13: | {{quotation|We didn’t know it, but it turns out that sitting around a table with folks while the MakerBot Cupcake CNC is puttering away and doing its thing and making objects appear where there were none before is really a great community activity! One of the gatherers mentioned that it felt like a geek campfire and it did!}} ([http://blog.makerbot.com/2009/04/27/maker-revolution-gathering-round-the-makerbot-campfire/ Pre Pettis], retrieved 13:43, 25 June 2009 (UTC)) | ||
Below are the fabbers most popular in June 2009. See also the links in the [[#Fab_Lab_portals_and_overviews general section]] above. All organizations and companies providing designs and selling parts or fully assembled tools do have web sites with a lot of information. | Below are the fabbers most popular in June 2009. See also the links in the [[#Fab_Lab_portals_and_overviews general section]] above. All organizations and companies providing designs and selling parts or fully assembled tools do have web sites with a lot of information. | ||
Line 279: | Line 285: | ||
* [http://blog.makerbot.com/ MakerBot Industries Blog] | * [http://blog.makerbot.com/ MakerBot Industries Blog] | ||
* Designs can be shared on [http://www.thingiverse.com/ thingyverse]. | * Designs can be shared on [http://www.thingiverse.com/ thingyverse]. | ||
[[image:candyfab6000.jpg|thumb|200px|right|The CandyFab 6000 sugar-based 3D printer]] | |||
;CandyFab | |||
* [http://www.candyfab.org/ CandyFab Project home page] | |||
* CandyFab kits should be available in fall 2009 from [http://evilmadscience.com/ Evil Mad Science]. The CanyFab 6000 prototype is shown to the right (click to enlarge). | |||
* [http://wiki.candyfab.org/ CandyFab Wiki] | |||
* [http://en.wikipedia.org/wiki/CandyFab CandyFab] (Wikipedia) | |||
* [http://forum.candyfab.org/ CandyFab Forum] | |||
; Other links | ; Other links | ||
Line 289: | Line 303: | ||
* [http://home.att.net/~castleisland/comp_lks.htm 3D Printer System Manufacturers - Systems for Less Than US$20,000] (parts for self-assembly can be as low as $600) | * [http://home.att.net/~castleisland/comp_lks.htm 3D Printer System Manufacturers - Systems for Less Than US$20,000] (parts for self-assembly can be as low as $600) | ||
* [http://www.desktopfactory.com/ Desktop Factory 125ci 3D Printer] (network compatible, about $5000, 1 cubic inch of "print" costs about $1). See also the [http://en.wikipedia.org/wiki/Desktop_Factory Wikipedia] entry. | * [http://www.desktopfactory.com/ Desktop Factory 125ci 3D Printer] (network compatible, about $5000, 1 cubic inch of "print" costs about $1). See also the [http://en.wikipedia.org/wiki/Desktop_Factory Wikipedia] entry. | ||
* [http://createitreal.com/pages/products.html CreateItReal] (Denmark) sells a 3D printer and a Laser Cuter, each for $5000. We found little information about these - [[User:Daniel K. Schneider|Daniel K. Schneider]] 13:43, 25 June 2009 (UTC). | |||
* [http://uprint.dimensionprinting.com/ uPrint] from Dimension (about £12'000). | * [http://uprint.dimensionprinting.com/ uPrint] from Dimension (about £12'000). | ||
* [http://www.objet.com/3D-Printer/Alaris30/ Alaris] from Object (price ???) | * [http://www.objet.com/3D-Printer/Alaris30/ Alaris] from Object (price ???) |
Revision as of 15:43, 25 June 2009
This article or section is currently under construction
In principle, someone is working on it and there should be a better version in a not so distant future.
If you want to modify this page, please discuss it with the person working on it (see the "history")
Introduction
A Fab Lab (fabrication laboratory) is a small-scale workshop with computer controlled tools with the aim to make "almost anything". (Wikipedia). The smallest type of a modern fab lab is a so-called 3D-printer. Fab labs are a disruptive technology.
See also: Constructionist learning objects and Fröbel gifts, i.e. educational application areas with huge potential for desktop fabbers. Disclaimer: I am not a "fab lab" expert and some technical information may be wrong. However, there should be enough good links that you could follow up - Daniel K. Schneider 13:43, 25 June 2009 (UTC).
Fab labs can have different aims, e.g. rapid prototyping or low cost and on-demand manufacturing from "open source designs" for both hobbyist and serious use. Both purposes include an idea of empowering individuals to create devices that are adapted to specific needs.
The Fab@Home project emphasizes freedom of design and innovation of a Solid Freeform Fabrication system:
In a similar way IFTF, in the Future of Making Map argues:
Finally, the topic of the LIFT France '09 conference was Hands-on future. According to Laurent Haug,
What happened in the software industry - young guys waking up with an idea, ending up changing the world from their sofa like it happened with Google, Amazon, Facebook, etc. - is now happening in the tangible world. Things like Arduino are enabling hackers and creators all around the globe, and what was possible with software (easily assemble code to create new applications) is now possible with objects. The conference program was centered around three main topics:
- Changing Things: Towards objects that are not just “smart” and connected, but also customizable, hackable, transformable, fully recyclable… Towards decentralized and multipurpose manufacturing, or even home fabrication…
- Changing Innovation: Towards continuous and networked innovation, emerging from users as well as entrepreneurs, from researchers as well as activists…
- Changing the Planet: Towards a “green design” that reconnects global environmental challenges with growth, but also with human desire, pleasure, beauty and fun ...
The first Fab Lab emerged at MIT under the direction of N. Gershenfeld. It included a laser cutter, a miniature milling machine and jigsaw cutting machine.
The Fab Lab movement also is anchored in ecological thinking. “Think of RepRap as a China on your desktop” (Chris di Bona). Materials used are no much polluting and there is no transportation cost.
A possible future was described by Vilbrandt et al (2008) “Advances in digital design and fabrication technologies are leading toward single fabrication systems capable of producing almost any complete functional object. We are proposing a new paradigm for manufacturing, which we call Universal Desktop Fabrication (UDF), and a framework for its development. UDF will be a coherent system of volumetric digital design software able to handle infinite complexity at any spatial resolution and compact, automated, multi-material digital fabrication hardware. This system aims to be inexpensive, simple, safe and intuitive to operate, open to user modification and experimentation, and capable of rapidly manufacturing almost any arbitrary, complete, high-quality, functional object. Through the broad accessibility and generality of digital technology, UDF will enable vastly more individuals to become innovators of technology, and will catalyze a shift from specialized mass production and global transportation of products to personal customization and point-of-use manufacturing. Likewise, the inherent accuracy and speed of digital computation will allow processes that significantly surpass the practical complexity of the current design and manufacturing systems. This transformation of manufacturing will allow for entirely new classes of human-made, peer-produced, micro-engineered objects, resulting in more dynamic and natural interactions with the world.” (Abstract, retrieved 13:43, 25 June 2009 (UTC)).
In october 2008, Evan Malone, the principal designer and implementor of Fab@Home, posted a (draft) Functional Block Diagram for FutureFab System at NextFab and that is shown below.
History
An excellent source for the early history of 3-D models is Lipson et al, 2004). According to this paper, “Physical models of machines have played an important role in the history of engineering for teaching, modeling, and exploring mechanical concepts. Many of these models have been replaced by computational representations, but new rapid-prototyping technology allows reintroduction of physical models as an intuitive way to demonstrate mechanical concepts” (Lipson et al, 2004:1032).
- 15th century
- Filippo Brunelleschi 1377–1436, the architect and engineer of the Duomo in Florence is
known to have created construction models.
- 19th century
- Robert Willis (1800–1875) of Cambridge was known for his kinematic teaching models.
- Franz Reuleaux (1829–1905) created the world’s largest collection of kinematic models at the Technical University of Berlin with over 800 models.
- 1940's
- Birth of numerical control, i.e. machine tools controlled by code.
- mid 1950's
- Birth of special purpose programming languages for computer numerical controlled (CNC) machine tools.
- end 1950's - mid 1960's
- Birth of interfaces of Computer-aided design (CAD) with CNC.
- 1970
- Mohamed Hashish created a technique to add abrasives to the water jet cutter
- 1986
- 3D-Printing
- 2005
- Neil Gershenfeld's et al. MIT class 863.04 - how to make (almost) anything.
- 2006
- The RepRap prototype
- 2007
- Neil Gershenfeld and Joe Jacobson MIT class How To Make Something That Makes (almost) Anything.
- The CandyFab Project
Hardware tools
There exist several popular fab lab technologies, some of which are described below in more details. Most fall in the category of solid freeform fabrication tools and that include:
- 3D printers
- Laser cutters
- CNC machines
- Automated paper cutters
- 3D Scanners (for replication)
- Laser sintering
Another set of toolkits are electronics platforms like Arduino.
A fabber (or digital fabricator) refers to a "factory in box" (i.e. one of the above tools) that can create things automatically from digital data. The Digital Fabrication Portal distinguishes three fundamental kinds of fabbers, according to the way they operate on their raw material:
- Subtractive: Material is carved away from a solid block, such as by milling, turning, or electrodischarge machining (EDM). Subtractive fabbers have been automated since the late 1940s, and are often called computer-numerically controlled (CNC) machines.
- Additive: Material is successively added into place to build up the desired object. The methods used include selective curing, selective sintering, and aimed deposition. The first commercial additive fabber was introduced in 1987. [This includes the 3D printers that became very cheap and popular in recent years] (DKS).
- Formative: Material is neither added nor removed, but opposing pressures are applied to the material to modify its shape. Techniques in this category, including automated bending and reconfigurable molding, are under development.
- Hybrid: Processes from two or more of the above categories are combined. Sheet-based fabbers, which cut and laminate successive layers of sheet material, are hybrid subtractive/additive devices. A combination CNC punch press and press brake is a hybrid subtractive/formative fabber. (retrieved 17:25, 24 June 2009 (UTC)).
Solid Freeform Fabrication overview

“Freeform Fabrication is a collection of manufacturing technologies with which parts can be created without the need for part-specific tooling. A computerized model of the part is designed. It is sliced computationally, and layer information is sent to a fabricator that reproduces the layer in a real material” (Laboratory of Freeform Fabrication, UTexas, retrieved 17:25, 24 June 2009 (UTC)). CreatItReal shows an animation of this principle. Typical commercial free form fabricators range between 20'000 and 300'000 $US although low-end 3D printers start at $5000 (June 2009). Open source kits are much cheaper if self-assembled (see below)
Currently, low-end commercial 3D prototypers are still costly for individuals who want to "play" or schools. On June 2009, the cheapest 3D printer we found a printer at $5000 from Desktop Factory and one at 5000 Euros from CreateItReal. A more expensive one is "Dimension uPrint" and cost £12000. In addition you need to buy materials and solidifiers which may be more expensive. According to Wikipedia (retrieved 17:25, 24 June 2009), “Prototypes made by these low-end commercial machines cost around US$2 per cubic centimeter to fabricate. The RepRap Project is on track to produce a 3D prototyping machine and free and open source accompanying software that costs about US$400 to build and which can fabricate objects at a cost of about US$0.02 per cubic centimeter.”
Low End Solid Freeform Fabrication tools, also called rapid prototype machines are usually a kind of 3D printers. “3D printing is a unique form of fabrication that is related to traditional rapid prototyping technology. A three dimensional object is created by layering and connecting successive cross sections of material. 3D printers are generally faster, more affordable and easier to use than other additive fabrication technologies. While prototyping dominates current uses, 3D printers offers tremendous potential for retail consumer uses.” (Wikipedia, retrieved 17:25, 24 June 2009 (UTC)).
There exist various kinds of 3D printers, e.g. Inkjet where layers of powder (e.g. plaster, corn starch or resins) are selectively bonded or photopolymer machines that fix liquids with an UV flood lamp. A low-cost fabber, typically includes a kind of "gun" that heats up polymer plastic from a filament and then extrudes a fine stream to build things. A similar more complex procedure is called fused deposition modeling (FDM) (Montaro, 2002) and is described more precisely by Lipson et al. (2004:1030): “The process creates a sequence of thermoplastic layers from a filament wound coil that is heated and extruded through a nozzle. The trajectory of the nozzle is derived from the triangle mesh, so as to raster scan and fill solid volumes. In order to create functioning mechanisms, a second, soluble release material is placed in the gaps between the movable parts.”
Low cost fabbers
Very low-cost non-proprietary 3D printers are often referred to as Fabbers (although the term includes other technologies, including high-end ones). There exist several projects with a high profile in the "web 2.0 sphere".
The Fab@Home project (retrieved June 2009) “is a project dedicated to making and using fabbers - machines that can make almost anything, right on your desktop. [...] Fabbers (a.k.a. 3D printers or rapid prototyping machines) are a relatively new form of manufacturing that builds 3D objects by carefully depositing materials drop by drop, layer by layer. With the right set of materials and a geometric blueprint, you can fabricate complex objects that would normally take special resources, tools and skills if produced using conventional manufacturing techniques. A fabber can allow you to explore new designs, email physical objects to other fabber owners, and most importantly - set your ideas free. Just as MP3s, iPods and the Internet have freed musical talent, we hope that blueprints and fabbers will democratize innovation.”. Fab@Home was conceived by Prof. Hod Lipson of Cornell University and designed and implemented by Evan Malone. Current developement includes more people.
RepRap is another well know project. “RepRap is short for Replicating Rapid-prototyper. It is the practical self-copying 3D printer shown on the right - a self-replicating machine. This 3D printer builds the parts up in layers of plastic. This technology already exists, but the cheapest commercial machine would cost you about €30,000. And it isn't even designed so that it can make itself. So what the RepRap team are doing is to develop and to give away the designs for a much cheaper machine with the novel capability of being able to self-copy (material costs are about €500). That way it's accessible to small communities in the developing world as well as individuals in the developed world. Following the principles of the Free Software Movement we are distributing the RepRap machine at no cost to everyone under the GNU General Public Licence. So, if you have a RepRap machine, you can use it to make another and give that one to a friend...” (What is RepRap?, retrieved 17:25, 24 June 2009 (UTC)).
The CandyFab project is a 3D freeform fabrication project that works with sugar and other low-melting point materials. This project is different from Fab@Home and RepRap in two ways. The fabricator can print a much larger printable volume but with a lower resolution and you may eat the product. The creators argue that “Sugar is a particularly good medium because it's easy to obtain, low in cost, kid friendly, water soluble, non-hazardous, non-toxic, non-intimidating, rigid despite having a low melting point, and may be suitable for making objects for lost sugar (like lost wax) investment casting. We also think that it may also be possible to make interesting food with this technology.” (Sneak preview: The Evil Mad Scientist 3D Printer Project, retrieved 13:43, 25 June 2009 (UTC)).
Until recently, fabbers had to be assembled by the end-user using open designs and low-level parts, i.e. many many days of bricolage. However, some fabbers now can be bought commercially as easy kits or fully assembled. E.g. in June 2009, the NextFab Store sold kits for about $3000 and assembled Fab@Homes for about $4000. Bits from Byte sold a (unassembled) ReRap kit (Version 3 - RapMan) for about £750. The latest addition as of June 2009 was the Cupcake from MakerBot Industries, sold £750 (unassembled).
Malone and Lipson (2007) published an interesting breakdown of the cost of the model 1 fab@home 3D printer. Part costs were about $2300 USD plus about 18 hours of assembly work.
Cutters
- Laser cutters and engravers
- Laser cutters and engravers can process any non-metal material (e.g. acrylic, ceramics, cork, fiberglass, glass, plastic, leather, paper, stone, wood). “Laser cutting is a technology that uses a laser to cut materials, which is used in the production line and is typically used for industrial manufacturing applications. Laser cutting works by directing the output of a high power laser, by computer, at the material to be cut. The material then either melts, burns, vaporizes away, or is blown away by a jet of gas, [1] leaving an edge with a high quality surface finish. Industrial laser cutters are used to cut flat-sheet material as well as structural and piping materials.” (Wikipedia, retrieved 17:25, 24 June 2009 (UTC)).
- Laminated Object Manufacturing (LOM)
- “Laminated object manufacturing (LOM) is a rapid prototyping system developed by Helisys Inc. (Cubic Technologies is now the successor organization of Helisys) In it, layers of adhesive-coated paper, plastic, or metal laminates are successively glued together and cut to shape with a knife or a laser cutter.” ([2])
- Plasma cutters
- “Plasma cutting is a process that is used to cut steel and other metals of different thicknesses (or sometimes other materials) using a plasma torch. In this process, an inert gas (in some units, compressed air) is blown at high speed out of a nozzle; at the same time an electrical arc is formed through that gas from the nozzle to the surface being cut, turning some of that gas to plasma. The plasma is sufficiently hot to melt the metal being cut and moves sufficiently fast to blow molten metal away from the cut. Plasma can also be used for plasma arc welding and other applications.” (Wikipedia, retrieved 17:25, 24 June 2009 (UTC)).
Plasma cutters come in various sizes are available from $3000.
- Water jet cutter
- “A water jet cutter is a tool capable of slicing into metal or other materials using a jet of water at high velocity and pressure, or a mixture of water and an abrasive substance. The process is essentially the same as water erosion found in nature but greatly accelerated and concentrated. It is often used during fabrication or manufacture of parts for machinery and other devices” (Wikipedia, retrieved 21:22, 23 June 2009 (UTC).)
According to Wikipedia, water jets can cut with a with of about 1mm and can cut materials such as rubber, foam, plastics, composites, stone, glass, tile, metals, food, paper and much more. Also, water jets can cut material without much harming or changing the materials' structures since there is no heat. I also can be considered a green technology, since it doesn't produce harmful waste. Water and abrasives can be recycled.
Selective Laser sintering
“In the Selective Laser Sintering (SLS) process, three-dimensional parts are created by fusing (or sintering) powdered thermoplastic materials with the heat from an infrared laser beam.” (Selective Laser Sintering (SLS), SLS Prototype, retrieved 17:25, 24 June 2009 (UTC)).
- “Selective laser sintering is an additive rapid manufacturing technique that uses a high power LASER (for example, a carbon dioxide laser) to fuse small particles of plastic, metal, ceramic, or glass powders into a mass representing a desired 3-dimensional object. The laser selectively fuses powdered material by scanning cross-sections generated from a 3-D digital description of the part” (Wikipedia, retrieved 17:25, 24 June 2009 (UTC)).
This technology looks rather complex and expensive, compared to low-end 3D printers...
Stereolithography (SLA)
Stereolithography (or photopolymerization) “is a common rapid manufacturing and rapid prototyping technology for producing parts with high accuracy and good surface finish. A device that performs stereolithography is called an SLA or Stereolithography Apparatus.” (Wikipedia, retrieved 17:25, 24 June 2009 (UTC)).
SLA is too expensive for fab labs (between $100,000 and $400,000)
CNC mills
A milling machine (fr. "fraiseuse") is a machine tool used for the shaping of metal and other solid materials. It uses rotating cutters to cut stuff from a workpiece. In more sophisticated milling machines, both the cutters and the workpiece can be rotated in three axis.
3D Scanners
An alternative to designing objects is to scan them. 3D scanners can be bought for about $3000.
Electronic kits
- Arduino
Arduino “is an open-source electronics prototyping platform based on flexible, easy-to-use hardware and software. It's intended for artists, designers, hobbyists, and anyone interested in creating interactive objects or environments.
Arduino can sense the environment by receiving input from a variety of sensors and can affect its surroundings by controlling lights, motors, and other actuators. The microcontroller on the board is programmed using the Arduino programming language (based on Wiring) and the Arduino development environment (based on Processing). Arduino projects can be stand-alone or they can communicate with software on running on a computer (e.g. Flash, Processing, MaxMSP).” (Arduino Home Page, retrieved 17:25, 24 June 2009 (UTC)).
Software
File formats
See also Computer-aided design and manufacturing (CAD/CAM)
- The .STL file format
- “An StL (“StereoLithography”) file is a triangular representation of a 3-dimensional surface geometry. The surface is tessellated or broken down logically into a series of small triangles (facets). Each facet is described by a perpendicular direction and three points representing the vertices (corners) of the triangle. These data are used by a slicing algorithm to determine the cross sections of the 3-dimensional shape to be built by the fabber” (The StL Format, retrieved 17:25, 24 June 2009 (UTC)).
CAD/CAM Software
See also Computer-aided design and manufacturing (CAD/CAM)
- ReplicatorG is the software that will drive your CupCake CNC, RepRap machine, or generic CNC machine. You feed it GCode, it parses the GCode, and then controls your machine via a driver. Its cross platform, easily installed, and is based on the familiar Arduino / Processing environments.
- CandyFab developed CandyFaboulous, written in Processing, an open source programming language and environment for people who want to program images, animation, and interaction.
Fab Labs and fabbers in education
Fab labs in education seem to follow to connected axis of development: Teaching design and producing models for teaching concepts.
Lipson et al. (2004:1032) reports on “the use of computer-aided modeling tools and rapid prototyping technology to document, preserve, and reproduce in three dimensions, historic machines, and mechanisms. We have reproduced several preassembled, fully functional historic mechanisms such as early straight line mechanisms, ratchets, pumps, clock escapements and counting devices, including various kinematic components such as links, joints, gears, worms, nuts, bolts, and springs.”. The authors also argue that “One can realize many historical concepts that exist only on paper, such as Leonardo da Vinci's slider crank mechanism, as well as other models that exhibit more contemporary concepts from aerodynamics to molecular biology.”
Fab labs were born in higher education (e.g. Gershenfeld:2005) and most of these are sponsored by academic institutions. Of course, technical hobbyists always did exist and and in many countries, schools do offer facilities and even classes for all sorts of bricolage. The most prominent fabber projects were founded by academics. E.g. Reprap by Adrien Bowyer et al. at University of Bath (UK); Fab@Home by Evan Malone while he was a PhD student at Cornell. Commercial low-cost printers are sold as tool for design classes. E.g. a Desktop Factory printer is advertised as “With the Desktop Factory 3D printer, departments within large firms will be able to have their own dedicated 3D printers, and many small businesses, design firms and schools will be able to own this capability for the first time. Professional designers, engineers and students alike will be able to build inexpensive models from their designs before committing to expensive, custom prototyping” (retrieved 13:43, 25 June 2009 (UTC)).
Knapp et al. (2007) stress the benefits of physical models in a variety of educational settings, e.g. Mathematics, anatonomy, molecular biology, aeronautics, chemistry, arehceology: “Physical models have been shown to enhance learning in general student populations as well. Students learn in a variety of ways, and models allow students to include their sense of touch in the learning experience. The role of experience is emphasized in Piaget's description of cognitive development, that is, to know an object a subject must act on it and thus transform it - displace, connect, combine, take apart, and reassemble it. (Cohen, 1983). Science education especially benefits from the use of models. "If one goal of science education is to enhance and maximize an individual's special conceptual ability, then access to manipulatives is advisable for those individuals. This access to manipulatives might also enhance development of their logical abilities... Internality is positively correlated with student achievement, and experience with manipulatives tends to move external subjects toward the internal end of the internal external continuum." (Cohen, 1982)”. Knapp et al. also stress the general benefits of models and manipulatives, quoting a study from Lillard (2006) showing that children from a Montessori kindergarten significantly outperformed their peers at traditional schools in standardized tests of reading and math.
The Tactilelearning.org stresses the importance of tactile models for the visually impaired and present several devices made "by hand" for teaching. A similar project is Touch Graphics that produced a number of projects, some of which are commercially available.
As the power of desktop fabbers will increase and cost decrease over the next few years, Lipson et al. (2004:1032) argue that {{quotation|more elaborate machines may be printable by a growing community around the world. Moreover, as new research leads to multimaterial functional freeform fabrication, we expect that incorporation of elastomers, lubricants, actuators, and sensors, electronics and power devices (Lipson, 2005b) will allow faithful replication and electronic sharing of an everincreasing scope of physical models and artifacts.
Links
Fab Lab portals and overviews
- FabCentral, The Center for Bits and Atoms, MIT.
- Fab Lab FAQ, MIT. (includes further pointers).
- How to make (almost) anything (alex schaub's mas863 log Fall 2008). Illustrates what could be done.
- RepRap (Main site)
- Wikipedia articles
- Wikipedia
- Category:Solid freeform fabrication (Wikipedia).
- Desktop manufacturing (Wikipedia)
- Digital fabricator (Wikipedia)
- Fabber (Wikipedia).
- Solid freeform fabrication (Wikipedia, overview).
- Overviews
- On the future of invention, by Neil Gershenfeld, Seedmagazine, June 24, 2009.
- Desktop manufacturing - Helping poor-world inventors, The Economist, Mar 23 2005.
- What is a Fabber?, An Introduction to the 21st Century, Ennex Corporation, retrieved 17:25, 24 June 2009 (UTC).
- In education
Repositories
Numerical control
- Numerical control (Wikipedia)
Cheap open source 3D printers
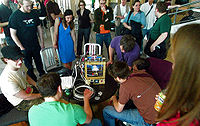
“We didn’t know it, but it turns out that sitting around a table with folks while the MakerBot Cupcake CNC is puttering away and doing its thing and making objects appear where there were none before is really a great community activity! One of the gatherers mentioned that it felt like a geek campfire and it did!” (Pre Pettis, retrieved 13:43, 25 June 2009 (UTC))
Below are the fabbers most popular in June 2009. See also the links in the #Fab_Lab_portals_and_overviews general section above. All organizations and companies providing designs and selling parts or fully assembled tools do have web sites with a lot of information.
- Fab@Home 3D printer
- Fab@Home, is a project dedicated to making and using fabbers - machines that can make almost anything, right on your desktop. This website provides everything you need to know in order to build or buy your own simple fabber, and to use it to print three dimensional object. Hardware designs and software on this website are open source.
- Designs are available from the Design Library
- Reprap 3D printer
- Bits from Bytes. Sells RepRap kits (£750).
- A1 Technologies. Sells Rapman systems (£750).
- RepRap Project (Wikipedia)
- Introduction to Reprap, retrieved 17:25, 24 June 2009 (UTC).
- RepRap Official Blog
- Designs can be shared on thingyverse.
- Cupcake (MakerBot Industries)
- Cupcake is a 3D printer that works with four kinds of plastic, e.g. ABS (Lego-like) and HDPE (milk-jug like). The founder of this company also is involved in the RepRap research project.
- MakerBot Industries sells CupCake (a 3D prototyper). It includes a Plastruder and an Arduino compatible microcontroller.
- CupCake CNC Basic Kit Product page ($750). A fully assembled tool costs $2'500.
- CupCake CNC overview.
- MakerBot Industries Blog
- Designs can be shared on thingyverse.
- CandyFab
- CandyFab Project home page
- CandyFab kits should be available in fall 2009 from Evil Mad Science. The CanyFab 6000 prototype is shown to the right (click to enlarge).
- CandyFab Wiki
- CandyFab (Wikipedia)
- CandyFab Forum
- Other links
- Three dimensional printing Laboratory (MIT,last update 2000)
Commercial entry-level 3D printers
- 3D Printer System Manufacturers - Systems for Less Than US$20,000 (parts for self-assembly can be as low as $600)
- Desktop Factory 125ci 3D Printer (network compatible, about $5000, 1 cubic inch of "print" costs about $1). See also the Wikipedia entry.
- CreateItReal (Denmark) sells a 3D printer and a Laser Cuter, each for $5000. We found little information about these - Daniel K. Schneider 13:43, 25 June 2009 (UTC).
- uPrint from Dimension (about £12'000).
- Alaris from Object (price ???)
- V-Flash from 3D Systems. (price about $10'000 ?)
Laser and plasma cutters
- How Plasma Cutters Work (Howstuffworks.com).
Water jets
CNC mills
Selective Laster Sintering (SLS)
Stereolithography (SLA)
- Stereolithography (SLA), Castle Island Co., retrieved 17:25, 24 June 2009 (UTC)
Arduino
- Arduino (Home page)
- YouTube Videos
New technology mags, blogs and communities
- SEED magazine
- NewScientist (tech section)
- FabLabs - a space for those tinkering with Fab Labs
- Thingiverse. Is a place for you to share your digital designs with the world.
- Hacked Gadgets
- NYC Resistor is a hacker collective with a shared space located in downtown Brooklyn.
- Next Big Future (blog)
- Pasta&Vinegar, Nicolas Nova, LiftLab (mind/tech bazar from outer space blog).
- The LIFT conference series (organized by our friends from LiftLab).
- Make magazine
Fab Labs
- Fab Academy (MIT) A news project in June 2009.
- Fablab Amsterdam
- Laboratory for Freeform Fabrication (UTexas).
Bibliography
- Burns M., (1995) The Freedom to Create, in Technology Management, Volume 1, Number 4 http://www.ennex.com/~fabbers/publish/199407-MB-FreedomCreate.asp
- Bowyer, Adrian (2007) Why Accountants are Dull and Guitarists are Glamourous - The End of Intellectual Property, Time Compression Technology Magazine, volume 15, issue 3, p33 (2007).
- Bowyer, Adrian (2007)- The Self-replicating Rapid Prototyper ─ Manufacturing for the Masses, Invited Keynote Address, Proc. 8th National Conference on Rapid Design, Prototyping & Manufacturing, Centre for Rapid Design and Manufacture, High Wycombe, June 2007. Rapid Prototyping and Manufacturing Association, ISBN-13: 978-0948314537 (2007).
- Bowyer, Adrian (2007). Breed your own Design, Icon Magazine, volume 52, October 2007.
- Ceccarelli, M., (Ed.) 2000, International Symposium on History of Machines
and Mechanisms, Proc. HMM Kluwer Academic, Dordrecht.
- Cohen D. L., Malone E., Lipson H., Bonassar L., (2006) "3D direct printing of heterogeneous tissue implants", Tissue Engineering, Vol. 12, No. 5: 1325-1335
- Cohen, H.G. (1983). A comparison of the affect of two types of student behavior with
manipulatives on the development of projective spatial structures. Journal of Research in Science Teaching, 20(9), 875-883
- Cohen, H.G. (1982). Relationship between locus of control and the development of spatial
conceptual abilities. Science Education, 66(4), 635-642
- Editors' Review (2005). Desktop Factories - FAB The Coming Revolution on Your Desktop -- from Personal Computers to Personal Fabrication By Neil Gershenfeld, Basic Books, Business Week, May 2 2005.
- Gershenfeld N. Think Globally, fabricate locally, PrincipalVoices.com. PDF (reprint)
- Gershenfeld, Neil, A., (2005) FAB: The Coming Revolution on Your Desktop – From Personal Computers to Personal Fabrication, Basic Books, ISBN 0-465-02745-8.
- Institute of the Future (2009). The future of making, PDF
- Jenweill, Mark, Fab Labs unshackle imaginations, USA Today, 11/6/2005.
- Moon, F. C., 2003a, Franz Reuleaux: Contributions to 19th Century Kinematics
and Theory of Machines, Applied Mechanics Reviews, American Society of Mechanical Engineers, N.Y.
- Lillard, A. and Else-Quest, N. (2006) The Early Years: Evaluating Montessori Education Science, Vol. 313. no. 5795, pp. 1893 - 1894
- Lipson H., Moon F.C., Hai J., Paventi C., (2004) 3D-Printing the History of Mechanisms,
ASME Journal of Mechanical Design, pp. 1029-1033. PDF
- Lipson H. (2005a) "Homemade: The future of Functional Rapid Prototyping", IEEE Spectrum, feature article, May 2005, pp. 24-31 http://www.mae.cornell.edu/ccsl/papers/Spectrum05_Lipson.pdf
- Lipson H. (2005b). "Homemade: The future of Functional Rapid Prototyping", IEEE Spectrum, feature article, May 2005, pp. 24-31.
- Lipson (2007), Printed 3D Models for Customized Hands-On Education. Proceedings of Mass
Customization and Personalization (MCPC) 2007.
- Knapp M., Wolff R., Lipson H. (2008), "Developing printable content: A repository for printable teaching models", Proceedings of the 19th Annual Solid Freeform Fabrication Symposium, Austin TX, Aug 2008. PDF.
- Lobovsky M., Lobovsky A., Behi M., Lipson H. (2008), "Solid Freeform Fabrication of Stainless Steel Using Fab@Home", Proceedings of the 19th Annual Solid Freeform Fabrication Symposium, Austin TX, Aug 2008. PDF
- Malone E., Lipson H., (2006) "Freeform Fabrication of Ionomeric Polymer-Metal Composite Actuators", Rapid Prototyping Journal, Vol. 12, No. 5, pp.244-253.
- Malone E., Lipson H., (2007) "Fab@Home: The Personal Desktop Fabricator Kit", Rapid Prototyping Journal, Vol. 13, No. 4, pp.245-255. PDF. (This is to our knowledge the best easy to read article explaining most aspects of a desktop fabricator).
- Malone E., Rasa K., Cohen D. L., Isaacson T., Lashley H., Lipson H., (2004) "Freeform fabrication of 3D zinc-air batteries and functional electro-mechanical assemblies", Rapid Prototyping Journal, Vol. 10, No. 1, pp. 58-69.
- Malone, E., Berry, M., Lipson, H., (2008), "Freeform Fabrication and Characterization of Zinc-air Batteries", Rapid Prototyping Journal, Vol. 14, No. 3, pp. 128-140. PDF
- McMains, S. (2005). "Layered Manufacturing Technologies", Comm. ACM, Volume 48, Number 6, pp 50-56.
- Montaro, M. et al., 2002, “Material Characterization of Fused Deposition Modeling (FDM) ABS by Designed Experiments,” University of California, Berkeley Report.
- Sells, Ed; Zach Smith, Sebastien Bailard, and Adrian Bowyer (2007). RepRap: The Replicating Rapid Prototyper - Maximizing Customizability by Breeding the Means of Production. Extended abstract in Proc. Mass Customization and Personalization Conference, MIT, October 2007.
- Thomson, Clive (2008). Build It. Share It. Profit. Can Open Source Hardware Work? Wired Magazine, 16:1
- Touchgraphics, Inc. (2009). An Interactive Talking Campus Model
at Carroll Center for the Blind, Final Report, center talking campus model final report low.pdf PDF. (Objects were created with a commercial 3D printer).
- Vilbrandt, T., Malone, E., Lipson H., Pasko, A., (2008) "Universal Desktop Fabrication", in Heterogeneous Objects Modeling and Applications, pp. 259-284. DOI: 10.1007/978-3-540-68443-5 (Access restricted)
- Wohlers, T. (2005). â3D Printing in Education: How High Schools, Colleges, and Universities
Leverage 3D Printing Technology.â Time-Compression Technologies, Sept/Oct 2005. HTML
- Links
- Adrian Bowyer's Publications
- Evan Malone's publications
- Cornell Computational Synthesis Laboratory publications
Acknowledgment
Thanx to Nicolas Nova for inviting me to LIFT France '09 which gave Daniel K. Schneider the impulse for writing a first version of this piece.